Gerry
Well-Known Member
]Hi
Been putting a new bathroom in so time has been short.
After looking at a few T wheels and seeing that most had a keyway location I decided that was not the way to go, so I went the long route started out making one. First problem was that I wanted a splined shaft and boss for an adjustable and strong fitting.
OK the column (internal) that i had with the correct splines for the steering rack is from a Formula Ford (roundy roundy racer) and did not have a splined top to it. Had to get a beer and think for a while at this point. I could have has a custom shaft made but finding someone who can do this in a reasonable time and price bracket was a no go. I decided the easiest place to get a matching boss and shaft was through a friend who supplies parts for Auto transmissions.
In the end I used an input shaft and the internal drive boss from a torque converter which gave me exactly what I needed. Now to join the original column and new shaft. To make sure there is no weak spots and I will always have a positive connection I made the two shafts an interference fit, cross drilled and pinned through both of them and then had it welded around the shoulder and on the ends of the pin.
One custom shaft with a splines boss for the wheel.
.
The next thing is the wheel itself. After playing around with a hose pipe cut to various diameters a final size was decided on. I drew the shape of the spider in Corel draw and off the the flame cutter where he cut the blank for me from 8mm thick MS plate.
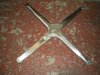
From here its a matter of welding in the boss, which I turned up to accept a torrington bearing on the lower side. This was then welded into the spider on both sides.
Now a lot of work with a power file to shape and smooth the spider. Probably around 12 hours. This left me with a flat spider which needed a bit of bending to form the double curve of a T wheel.
I made a hard wood profile of the double bend (took about 10 minuets) put it a vice and then heated each spider arm and bent it over the former... with help from my build buddy John.
A few adjustments to get them all the same and we have a T spider in a raw state.
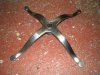
Final step is to polish it so a shinny finish and then brass plate with a home plating kit. All done.
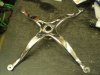
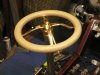
See its 'simple' I will cover the rim and brass nut next time. Hope this is all useful to someone
Gerry
Been putting a new bathroom in so time has been short.
After looking at a few T wheels and seeing that most had a keyway location I decided that was not the way to go, so I went the long route started out making one. First problem was that I wanted a splined shaft and boss for an adjustable and strong fitting.
OK the column (internal) that i had with the correct splines for the steering rack is from a Formula Ford (roundy roundy racer) and did not have a splined top to it. Had to get a beer and think for a while at this point. I could have has a custom shaft made but finding someone who can do this in a reasonable time and price bracket was a no go. I decided the easiest place to get a matching boss and shaft was through a friend who supplies parts for Auto transmissions.
In the end I used an input shaft and the internal drive boss from a torque converter which gave me exactly what I needed. Now to join the original column and new shaft. To make sure there is no weak spots and I will always have a positive connection I made the two shafts an interference fit, cross drilled and pinned through both of them and then had it welded around the shoulder and on the ends of the pin.
One custom shaft with a splines boss for the wheel.
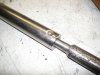
The next thing is the wheel itself. After playing around with a hose pipe cut to various diameters a final size was decided on. I drew the shape of the spider in Corel draw and off the the flame cutter where he cut the blank for me from 8mm thick MS plate.
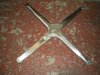
From here its a matter of welding in the boss, which I turned up to accept a torrington bearing on the lower side. This was then welded into the spider on both sides.
Now a lot of work with a power file to shape and smooth the spider. Probably around 12 hours. This left me with a flat spider which needed a bit of bending to form the double curve of a T wheel.
I made a hard wood profile of the double bend (took about 10 minuets) put it a vice and then heated each spider arm and bent it over the former... with help from my build buddy John.
A few adjustments to get them all the same and we have a T spider in a raw state.
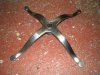
Final step is to polish it so a shinny finish and then brass plate with a home plating kit. All done.
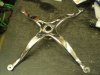
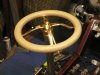
See its 'simple' I will cover the rim and brass nut next time. Hope this is all useful to someone
Gerry