Gerry
Well-Known Member
Good morning guys.
Bathroom all in just the pretty bits left.
In the last part I talked about the steering shaft length. What I did not tell you was the time we spent with various cushions and column heights before we finally committed to welding the shaft.
The stainless steel outer can be trimmed to length when all the other bits are done. The wooden rim for the wheel was outsourced to a guy how machine it to my drawings. The brass nut I machine myself so it looked right and the flange covered all the weld marks. (I dont like grinding welds on anything critical).
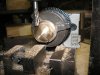
Now it was time to figure out the two control levers and the brass boss under the wheel. I started by turning the top section of the brass boss up. Being careful to make it a good fit on the stainless steel outer. This is the time to make some sketches and figure out how its going to be fitted. The best bit of all this is that you are doing it for yourself so not much to worry about with regard to following someone else's drawings. If it looks too big - back to the lathe and remachine. To me the way it looks is as important as its functionality.
Once this looked ok I turned a bottom ring which uses 3 bolts upwards into the boss. Careful drilling and tapping here as there was not much material to work with. The reason I did it this way was to allow for the fitting of the levers. The pic explain better than words.
I then had a think about 'bearing for the steering shaft and decided to turn them out of Teflon stock. One for the bottom and one for the top. As they were a good tight fit in to the Stainless outer it allowed me to move them up and down until they were in just the right place. The top one is secured by the 3 bolts through the side of the brass Boss, the bottom one by a single bolt throught the satinless. Be warned teflon is very proned to fluctuations in size depending on temperature and humidity so i had to 'wipe' the internal diameter several times to get a good smooth action without binding.
With the brass boss fitted and the bearing running OK a trial fit of this assembly in the car (Just bolting the bottom flange plate to the chassis bracket) meant I could get the height just right. This is done by trimming the outer stainless until the wheel sits exactly right. I wanted it to be high enough to clear my knees, allow a comfortable height for my arms to reach and move without fouling anything.
I know this sounds like a LOT of messing around but its worth every hour. I have driven a fair number of Rods and some are so uncomfortable it just make you want to get out and have a rest every 5 miles.
Now its time to turn to the control levers and their linkage. I allowed enough size on the outer column and the teflon bearings to run two shafts down in between the inner steering shaft and the outer tube.
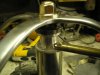
Again by trying out the set up, the length of the two levers was decide on I used a bit of 1/8 welding wire bent and cut to length. Its back to the lathe now to taper turn the levers and form the rounded end. I left a fair amount of extra length to aid the next step. Once these were turned I carefully put them in a vice and cold bent them to shape.
I think that enough for now so i will finish with a picture of the parts of the lever set up and column top.
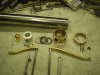
Hope you enjoyed and it has helped someone
Gerry
Bathroom all in just the pretty bits left.
In the last part I talked about the steering shaft length. What I did not tell you was the time we spent with various cushions and column heights before we finally committed to welding the shaft.
The stainless steel outer can be trimmed to length when all the other bits are done. The wooden rim for the wheel was outsourced to a guy how machine it to my drawings. The brass nut I machine myself so it looked right and the flange covered all the weld marks. (I dont like grinding welds on anything critical).
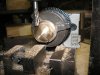
Now it was time to figure out the two control levers and the brass boss under the wheel. I started by turning the top section of the brass boss up. Being careful to make it a good fit on the stainless steel outer. This is the time to make some sketches and figure out how its going to be fitted. The best bit of all this is that you are doing it for yourself so not much to worry about with regard to following someone else's drawings. If it looks too big - back to the lathe and remachine. To me the way it looks is as important as its functionality.
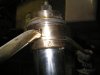
Once this looked ok I turned a bottom ring which uses 3 bolts upwards into the boss. Careful drilling and tapping here as there was not much material to work with. The reason I did it this way was to allow for the fitting of the levers. The pic explain better than words.
I then had a think about 'bearing for the steering shaft and decided to turn them out of Teflon stock. One for the bottom and one for the top. As they were a good tight fit in to the Stainless outer it allowed me to move them up and down until they were in just the right place. The top one is secured by the 3 bolts through the side of the brass Boss, the bottom one by a single bolt throught the satinless. Be warned teflon is very proned to fluctuations in size depending on temperature and humidity so i had to 'wipe' the internal diameter several times to get a good smooth action without binding.
With the brass boss fitted and the bearing running OK a trial fit of this assembly in the car (Just bolting the bottom flange plate to the chassis bracket) meant I could get the height just right. This is done by trimming the outer stainless until the wheel sits exactly right. I wanted it to be high enough to clear my knees, allow a comfortable height for my arms to reach and move without fouling anything.
I know this sounds like a LOT of messing around but its worth every hour. I have driven a fair number of Rods and some are so uncomfortable it just make you want to get out and have a rest every 5 miles.
Now its time to turn to the control levers and their linkage. I allowed enough size on the outer column and the teflon bearings to run two shafts down in between the inner steering shaft and the outer tube.
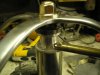
Again by trying out the set up, the length of the two levers was decide on I used a bit of 1/8 welding wire bent and cut to length. Its back to the lathe now to taper turn the levers and form the rounded end. I left a fair amount of extra length to aid the next step. Once these were turned I carefully put them in a vice and cold bent them to shape.
I think that enough for now so i will finish with a picture of the parts of the lever set up and column top.
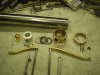
Hope you enjoyed and it has helped someone
Gerry