Gerry
Well-Known Member
Sorry but this has been bothering me for a few days
Its NOT a criticism, just an observation, but the thread look very flat. There seems to be no peaks on each thread and that worries me.
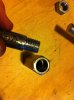
To get the max strength from a thread it needs to be formed with a good profile. If the peak (or point) of the thread is flat there is something wrong.
So now we got to get in to taps and dies.
In general the dies with a hex outside are 'dressing' dies and low cost. That is they are designed to dress or reform threads. If you want to cut a thread from a piece of bar you use split dies. Thats the ones with a round outside and a slot in them with a screw that allows adjustment for diameter differences. I payed 20 bucks for a set of 1/2 inch UNC taps and another 12 bucks for the die. Now think about the number of different sizes you are going to use and the price of premium stuff is not that bad.
There are 2 types of threads. Cut and Rolled. Rolled are the strongest but not really achievable at home, So we go for cut threads. Now here is where its get to 'You get what you pay for'
I have a set or 3 of the hex dies and use them to run down thread that are a bit tired, and thats all I use them for!!!
If I am cutting a new thread on fresh bar I always USE a premium brand split dies such as Dormer. You will feel the difference when you cut the thread.I also have the advantage of a Lathe which means I can chuck up the bar and use the tailstock to centre the die on the bar which gives me a true and parallel thread.
If the thread 'wobbles' over it length... its NOT a good one.
There is also screw cutting, but thats another ball park all together
Spend a little it will pay you back in peace of mind
Gerry
Its NOT a criticism, just an observation, but the thread look very flat. There seems to be no peaks on each thread and that worries me.
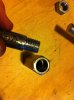
To get the max strength from a thread it needs to be formed with a good profile. If the peak (or point) of the thread is flat there is something wrong.
So now we got to get in to taps and dies.
In general the dies with a hex outside are 'dressing' dies and low cost. That is they are designed to dress or reform threads. If you want to cut a thread from a piece of bar you use split dies. Thats the ones with a round outside and a slot in them with a screw that allows adjustment for diameter differences. I payed 20 bucks for a set of 1/2 inch UNC taps and another 12 bucks for the die. Now think about the number of different sizes you are going to use and the price of premium stuff is not that bad.
There are 2 types of threads. Cut and Rolled. Rolled are the strongest but not really achievable at home, So we go for cut threads. Now here is where its get to 'You get what you pay for'
I have a set or 3 of the hex dies and use them to run down thread that are a bit tired, and thats all I use them for!!!
If I am cutting a new thread on fresh bar I always USE a premium brand split dies such as Dormer. You will feel the difference when you cut the thread.I also have the advantage of a Lathe which means I can chuck up the bar and use the tailstock to centre the die on the bar which gives me a true and parallel thread.
If the thread 'wobbles' over it length... its NOT a good one.
There is also screw cutting, but thats another ball park all together
Spend a little it will pay you back in peace of mind
Gerry