Keeper
Active Member
Today I finished making the headlight stands. I was going to buy some, but I couldn't find any I liked, so I made my own.
I used:
3/8 plate for the top and bottom, 1 inch .188 wall tube for the legs and 1.5 inch .120 wall for the light mount.
I am a couple steps into it when I took these pics as I tend to forget to take pics once I am working.
It took me longer setting up my little jig then it did to make the mounts! This is to make sure they both match.
I still have some final welding and clean up to do, but they turned out pretty well.
As you can see the tops are rounded, the inside has a rounded hole as well, this allows me to use the original rounded washers for adjustments, I have a ton of adjustment built into these lamps.
Some of you may remember my tape, well it was still there and I hit it pretty much bang on where I wanted them.
Had to check to make sure the tires were not going to hit, I knew they would not, but checked anyway!
The full front shot is a little fish eyed, I was not about to open the garage door and let out all the heat!!
The just because shot...
One more step down.
I used:
3/8 plate for the top and bottom, 1 inch .188 wall tube for the legs and 1.5 inch .120 wall for the light mount.
I am a couple steps into it when I took these pics as I tend to forget to take pics once I am working.
It took me longer setting up my little jig then it did to make the mounts! This is to make sure they both match.


I still have some final welding and clean up to do, but they turned out pretty well.
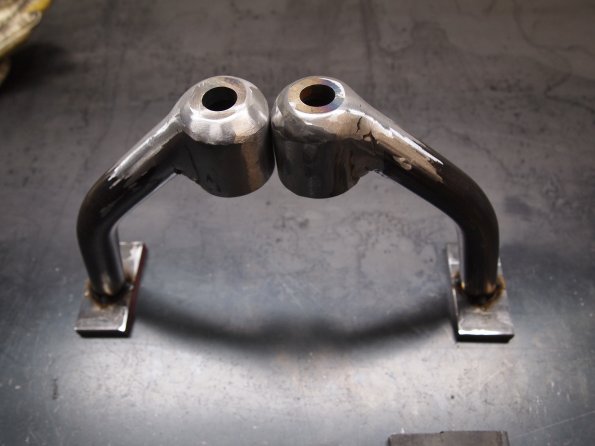
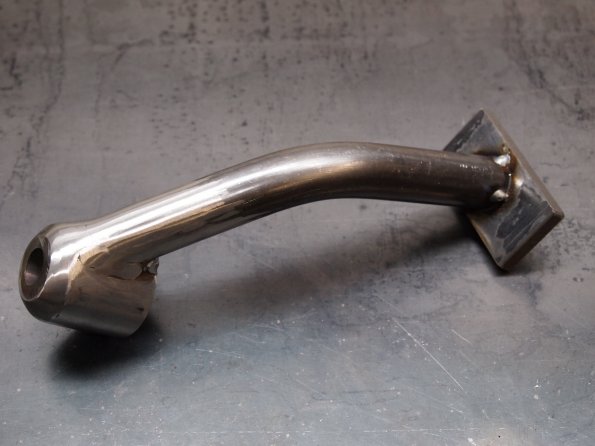
As you can see the tops are rounded, the inside has a rounded hole as well, this allows me to use the original rounded washers for adjustments, I have a ton of adjustment built into these lamps.

Some of you may remember my tape, well it was still there and I hit it pretty much bang on where I wanted them.


Had to check to make sure the tires were not going to hit, I knew they would not, but checked anyway!

The full front shot is a little fish eyed, I was not about to open the garage door and let out all the heat!!

The just because shot...
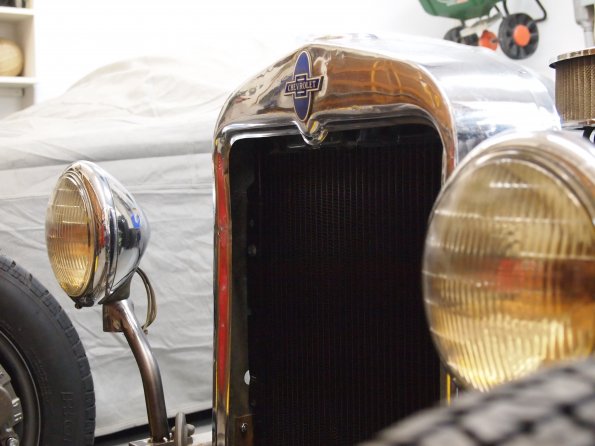
One more step down.