Indycars
Well-Known Member
I will just get this out of way now. These are guys that live 3D printing every day. I have found them to have very nice presentations.
https://www.youtube.com/channel/UCb8Rde3uRL1ohROUVg46h1A
https://www.youtube.com/channel/UCbgBDBrwsikmtoLqtpc59Bw
https://www.youtube.com/c/3DPrinterGuides/videos
https://www.youtube.com/c/AlexKenis/videos [This guy can be funny sometimes]
https://www.youtube.com/c/ChrisRiley/videos
I am going to just jump right in without trying to cover the basics in a logical order. I see this thread not as a complete analysis of 3D printing, that’s going to take you from the beginning to end. But just the things I am printing, problems I encounter and the process to get from idea to finish print. More of a journal.
I have already done a couple of projects, which you can find in the link below.
Wanted - Enclosed Car Trailer
The first print for this thread is going to help me with the installation of a transmission cooler in my tow vehicle the Lincoln Navigator. The frame is not flat across the top, nor is it perpendicular to the engine’s radiator. Therefore, I need to print a wedge that has an angle of 20.5°. But first a photo to give you an overall view of the project and the problem I need to solve. Nothing very complicated to model.
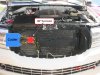
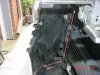
To print something, you first have to create your part in a 3D CAD software. I’m using FreeCAD since I believe it’s my best bet to learn a software that WILL ALWAYS BE FREE! It’s also a Parametric Modeler which I like.
FreeCAD: Your own 3D parametric modeler
Parametric vs. Direct Modeling | PTC
Once you have a 3D model, then you will have to export the file to STL or something similar. It is this file that you will open in the SLICER SOFTWARE (SS). Once I had it open in CURA (My SS), then I can slice the object and send it to my printer.
Ultimaker Cura: Powerful, easy-to-use 3D printing software
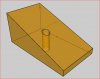
For the majority of parts printed there is Post Processing (PP). Could be cosmetic or for dimensional needs. Typically holes need to be opened up with the correct size drill bit. This time I got one end too long, so instead of printing another wedge, I just cut off one end with a hacksaw.
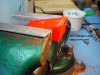
Problem solved although the angle should have been more like 19°, hard to measure an angle on a rounded surface. Yes, the aluminum angle is over kill (2" x 3" x 3/16"), but it’s what I already had. Posting Processing (PP) will be used even more in the 2nd part printed for the trans cooler.
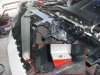
There are details that are not included above, but if you keep reading I will cover most of them eventually. Again I’m not trying to publish an article that is logical and steps thru the processing in order, that would take too much effort. But if this is something that you really want to try, then over time I will cover most of those details. Also you can do some of your own research using the links at the beginning of this post.
Be sure to share any experiences you have !
Hope you enjoyed this post in what I hope to be many over time!
.
https://www.youtube.com/channel/UCb8Rde3uRL1ohROUVg46h1A
https://www.youtube.com/channel/UCbgBDBrwsikmtoLqtpc59Bw
https://www.youtube.com/c/3DPrinterGuides/videos
https://www.youtube.com/c/AlexKenis/videos [This guy can be funny sometimes]
https://www.youtube.com/c/ChrisRiley/videos
I am going to just jump right in without trying to cover the basics in a logical order. I see this thread not as a complete analysis of 3D printing, that’s going to take you from the beginning to end. But just the things I am printing, problems I encounter and the process to get from idea to finish print. More of a journal.
I have already done a couple of projects, which you can find in the link below.
Wanted - Enclosed Car Trailer
The first print for this thread is going to help me with the installation of a transmission cooler in my tow vehicle the Lincoln Navigator. The frame is not flat across the top, nor is it perpendicular to the engine’s radiator. Therefore, I need to print a wedge that has an angle of 20.5°. But first a photo to give you an overall view of the project and the problem I need to solve. Nothing very complicated to model.
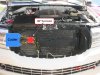
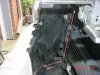
To print something, you first have to create your part in a 3D CAD software. I’m using FreeCAD since I believe it’s my best bet to learn a software that WILL ALWAYS BE FREE! It’s also a Parametric Modeler which I like.
FreeCAD: Your own 3D parametric modeler
Parametric vs. Direct Modeling | PTC
Once you have a 3D model, then you will have to export the file to STL or something similar. It is this file that you will open in the SLICER SOFTWARE (SS). Once I had it open in CURA (My SS), then I can slice the object and send it to my printer.
Ultimaker Cura: Powerful, easy-to-use 3D printing software
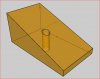
For the majority of parts printed there is Post Processing (PP). Could be cosmetic or for dimensional needs. Typically holes need to be opened up with the correct size drill bit. This time I got one end too long, so instead of printing another wedge, I just cut off one end with a hacksaw.
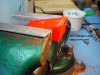
Problem solved although the angle should have been more like 19°, hard to measure an angle on a rounded surface. Yes, the aluminum angle is over kill (2" x 3" x 3/16"), but it’s what I already had. Posting Processing (PP) will be used even more in the 2nd part printed for the trans cooler.
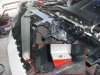
There are details that are not included above, but if you keep reading I will cover most of them eventually. Again I’m not trying to publish an article that is logical and steps thru the processing in order, that would take too much effort. But if this is something that you really want to try, then over time I will cover most of those details. Also you can do some of your own research using the links at the beginning of this post.
Be sure to share any experiences you have !
Hope you enjoyed this post in what I hope to be many over time!
.
Last edited: