Ted Brown
Member
Well I see a lot of (TUB) axles that have the bosses welded in with not very much of a notch into the axle, almost looks like a butt weld... I have over the years seen way to many bosses broken out of axles because of either poor welds or the car hit a bad bump, a chuck hole or maybe even bumped a curb while parking... not to forget some like doing wheelies
If a person is wanting to do wheelies or run your car real hard, it is a very good idea to flag the bosses... By this I mean = welding a flap of 1/4" steel to the boss (like a flag) before welding the boss into the cut out (notch)in the axle, cut slots for the flag to slide into, then it all can be welded into one strong piece. I also turn down all my bosses to 1 1/4" OD, this way I can get a good wrap around the boss with the axle material, when finished there is only about 5/8" gap between the two side flaps of the axle when welded around the boss... This is very good insurance for keeping that boss in place... I learned this from my tube bender Friend, He bent all my axles over the years, plus they welded up many axles for other business and did many sprint cars, which use flagged bosses in every case... You can clean up the added weld, (and flag material) so as not to have it look obvious to anyone, as long as it was V-ed out real good before welding... This is how I have been making axles all these years, and not to put down the way other's do their axles, as maybe they have used their own way of making sure their bosses stay put, because I see most all axles are done with no wrap to speak of, and they are still running after many years also... Thanks for letting me express my view on this matter
I will try and post a pic of a welded axle boss that is wrapped like this...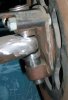


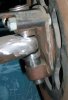