Because of my health issues, I've put the next step in my project (having the frame built) on hold. The frame I was going with would be a lot of compromises from what I had originally envisioned. So since I have nothing better to do, I decided to fire up DraftSight and see if starting from scratch I could come up with a frame layout that would be less of a compromise.
To ease getting in & out with my mobility issues, in the door area I need the top of the frame rails to be at 12" or less high. On the compromised design I was going to go with, the best I could do is around 15"...requiring an automated air ride suspension on the rear to make the car "kneel" while getting in & out. The limiting factor being the angle and height of the rear kickup. Most of the T-Bucket frames I've seen have kickups at around 7"-10" at 45° or 60°. The compromised design I was going with would be 7" at 45°.
The design I'm playing with now would have a kickup around 10"-11" at 80°. I have seen rat rod frames with the kickup at or near vertical, and over a foot or more high...but rat rods don't have a popular rep for sound engineering. Given that the car I'm planning will be short wheelbase, light weight, and low power...would the 11"/80° combo require additional bracing and/or gusseting?
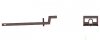
To ease getting in & out with my mobility issues, in the door area I need the top of the frame rails to be at 12" or less high. On the compromised design I was going to go with, the best I could do is around 15"...requiring an automated air ride suspension on the rear to make the car "kneel" while getting in & out. The limiting factor being the angle and height of the rear kickup. Most of the T-Bucket frames I've seen have kickups at around 7"-10" at 45° or 60°. The compromised design I was going with would be 7" at 45°.
The design I'm playing with now would have a kickup around 10"-11" at 80°. I have seen rat rod frames with the kickup at or near vertical, and over a foot or more high...but rat rods don't have a popular rep for sound engineering. Given that the car I'm planning will be short wheelbase, light weight, and low power...would the 11"/80° combo require additional bracing and/or gusseting?
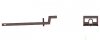