Keeper
Active Member
So I made my own headlight mounts, I set them up so I could either weld them on to the frame, or bolt on to the frame.
I still have to shape the bases, but I wanted to decide if I am going to bolt/weld them on first. That will determine the final shape.
So what do you suggest? Bolt or Weld?
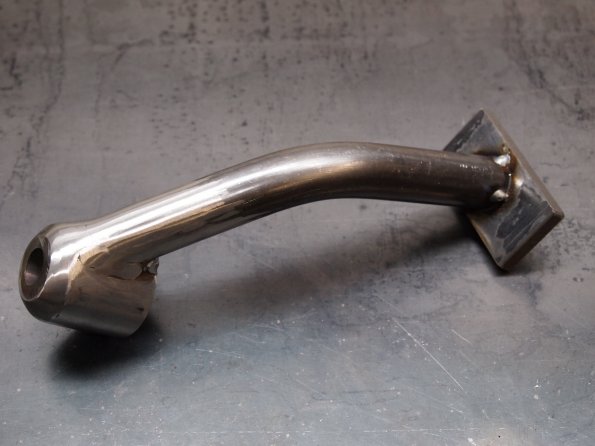
I still have to shape the bases, but I wanted to decide if I am going to bolt/weld them on first. That will determine the final shape.
So what do you suggest? Bolt or Weld?