Tbuilder
Active Member
I moved the engine/tranny to the right an inch to have it line up better to the pinion offset in the rear axle. This also has the advantage of leaving more room on the left side of the engine for the steering, ignition and the carb/intake manifold. One cannot tell it is offset without looking at it very carefully.
The cross member for the small block Ford with the C-4 transmission fit perfectly.
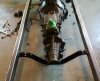
The cross member for the small block Ford with the C-4 transmission fit perfectly.