Once i finished the door handles i realised that i would need some matching door mirrors, found some the right shape but when i drilled the mirror arm the die cast was aweful, so decided to make some.
First a piece of 10mm stainless bar was drilled for the tail scallop, then it was cut in half so each half had a semi circle in it.
The upright is made from 6mm plate, all stainless is 316L
Next the basic shaped was cut and ground with a 1mm cutting disc and a flap disc in a angle grinder. The other parts were cut out, drilled and turned ready for welding together, the parts were polished before welding so only the welds needed blending and fettling.
Next the edes were chamfered several times till a 50p shape was acheived, then the edges were soft sanded till smooth and radiused.
The reverse side had to be hollowed out as this sit on a swage line so again the back was ground away to suit.
2 x 6.8mm holes were drilled and tapped 8mm for mounting studs, the long bolts are temporary and for holding during the polishing process.
All the parts were then TIG welded together, a fair bit of rod was used so i had something to get a nice radius with.
The finished Mirrors.
________________
First a piece of 10mm stainless bar was drilled for the tail scallop, then it was cut in half so each half had a semi circle in it.
The upright is made from 6mm plate, all stainless is 316L
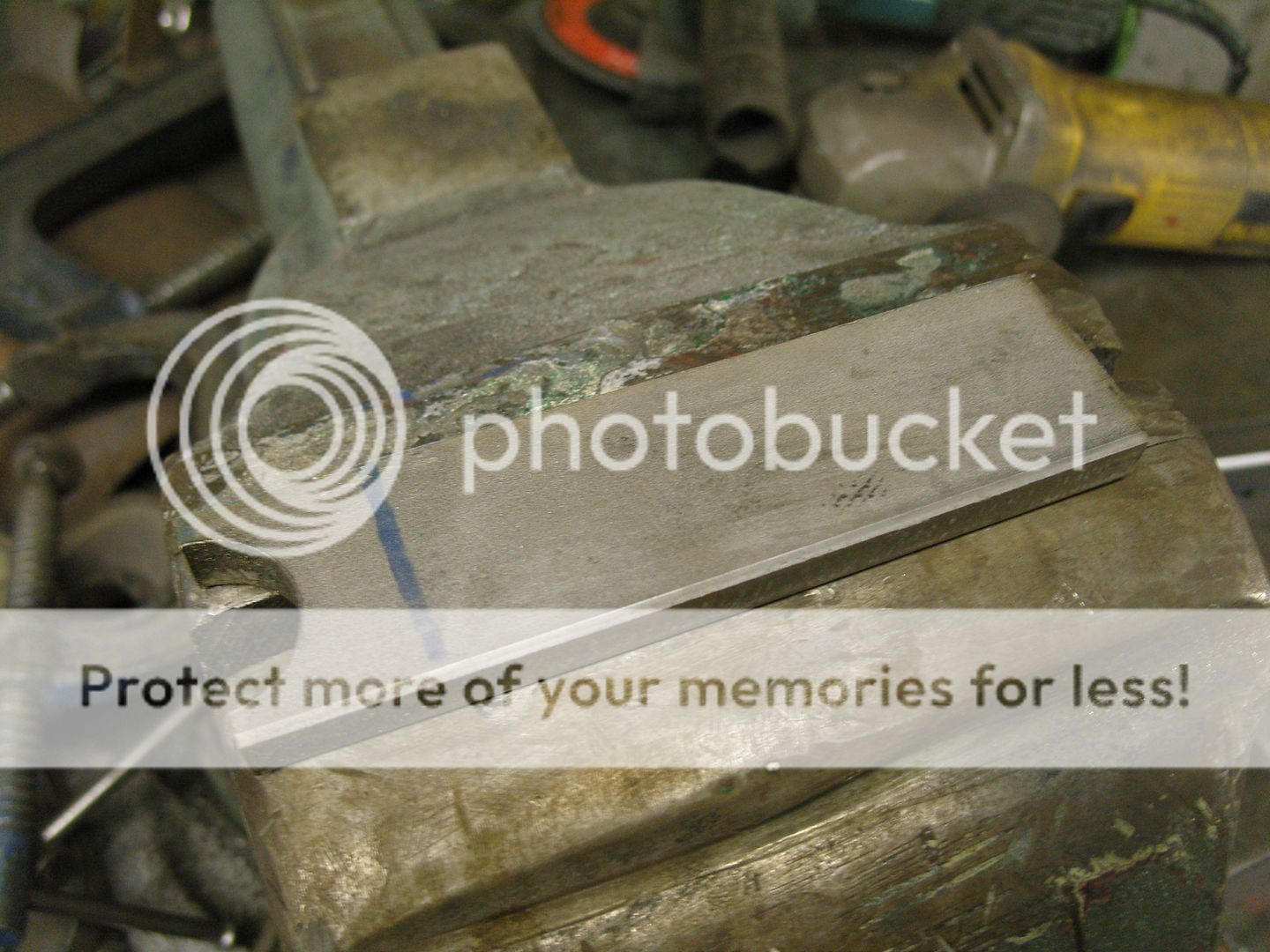
Next the basic shaped was cut and ground with a 1mm cutting disc and a flap disc in a angle grinder. The other parts were cut out, drilled and turned ready for welding together, the parts were polished before welding so only the welds needed blending and fettling.
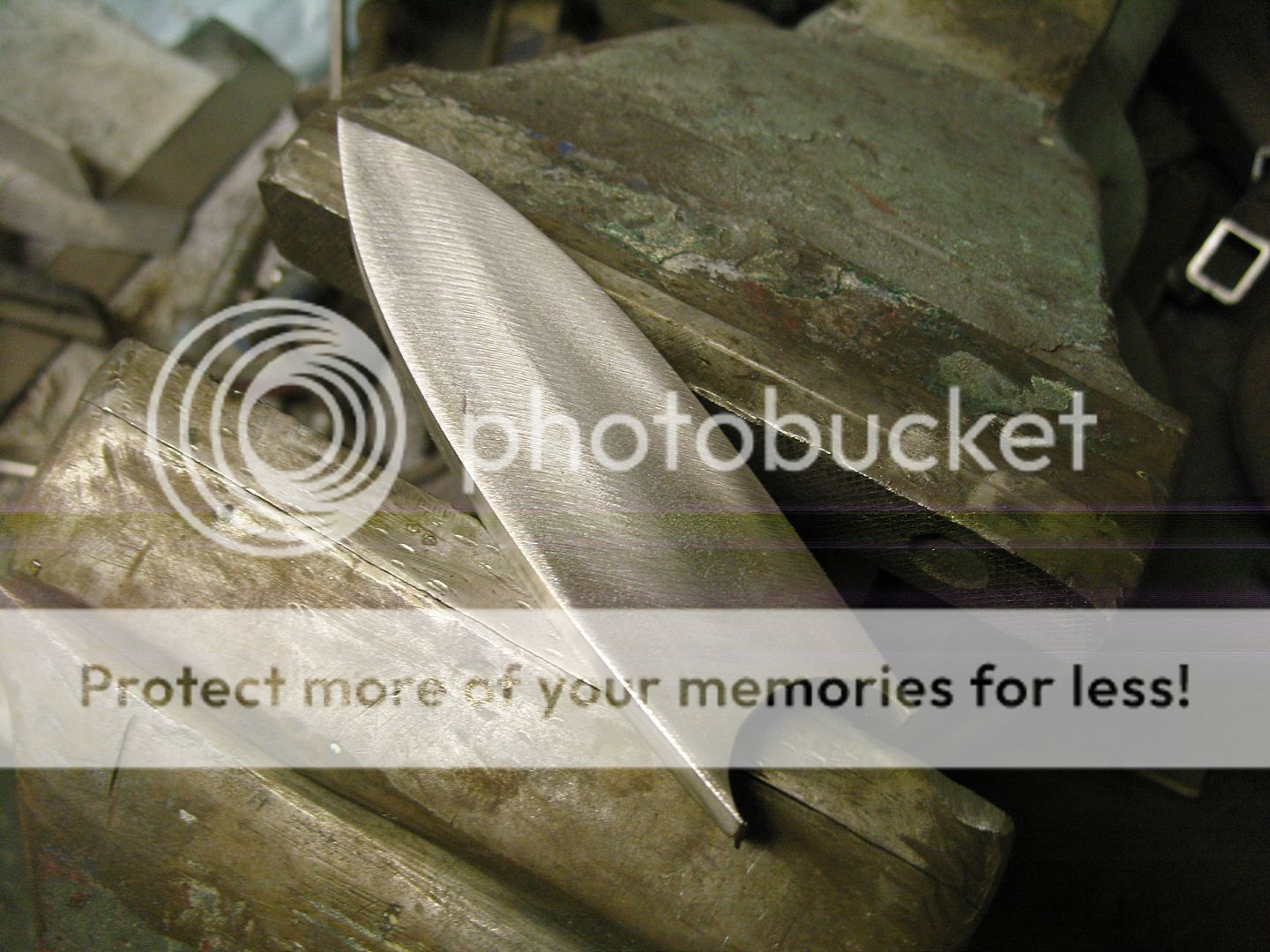
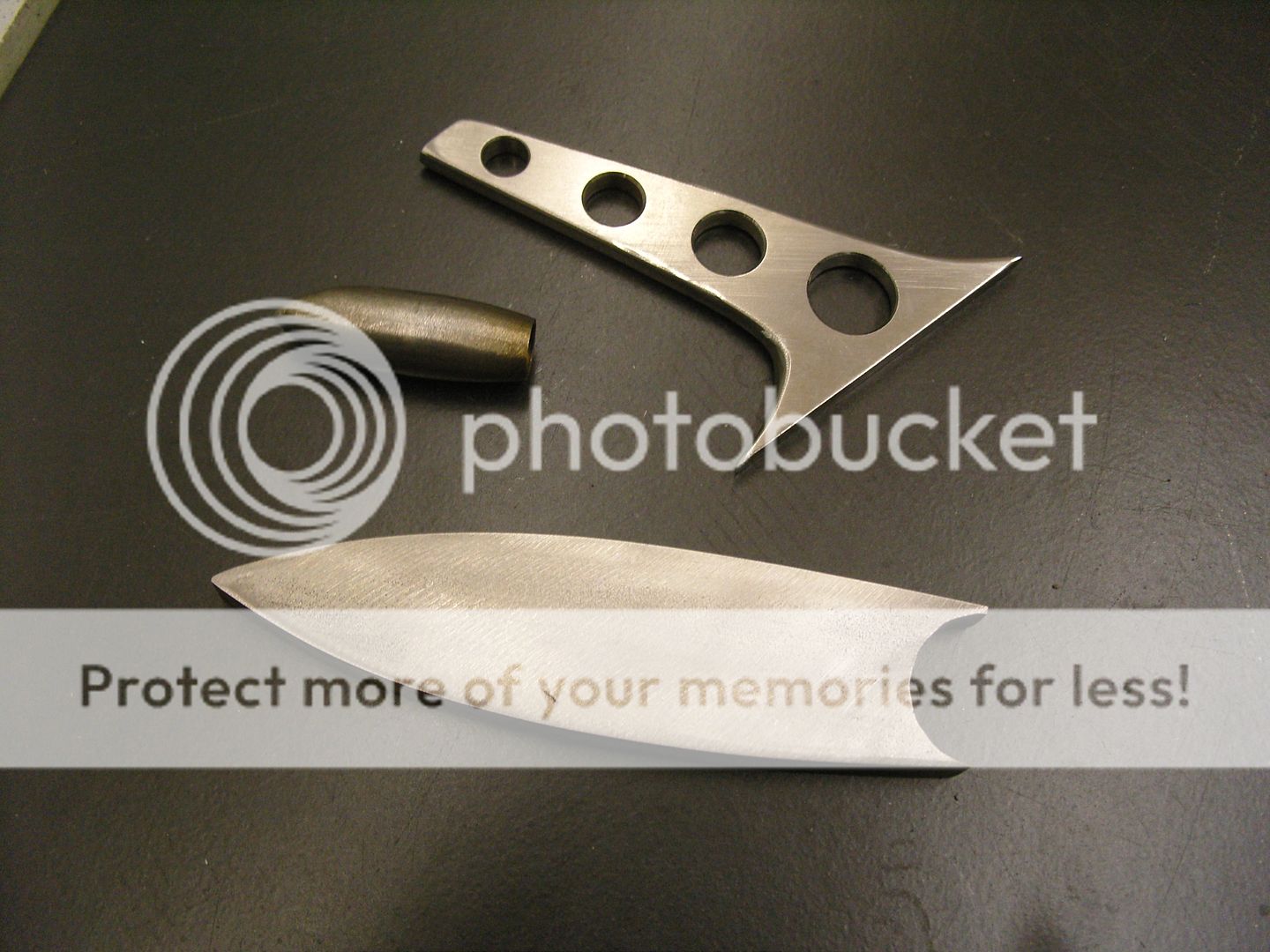
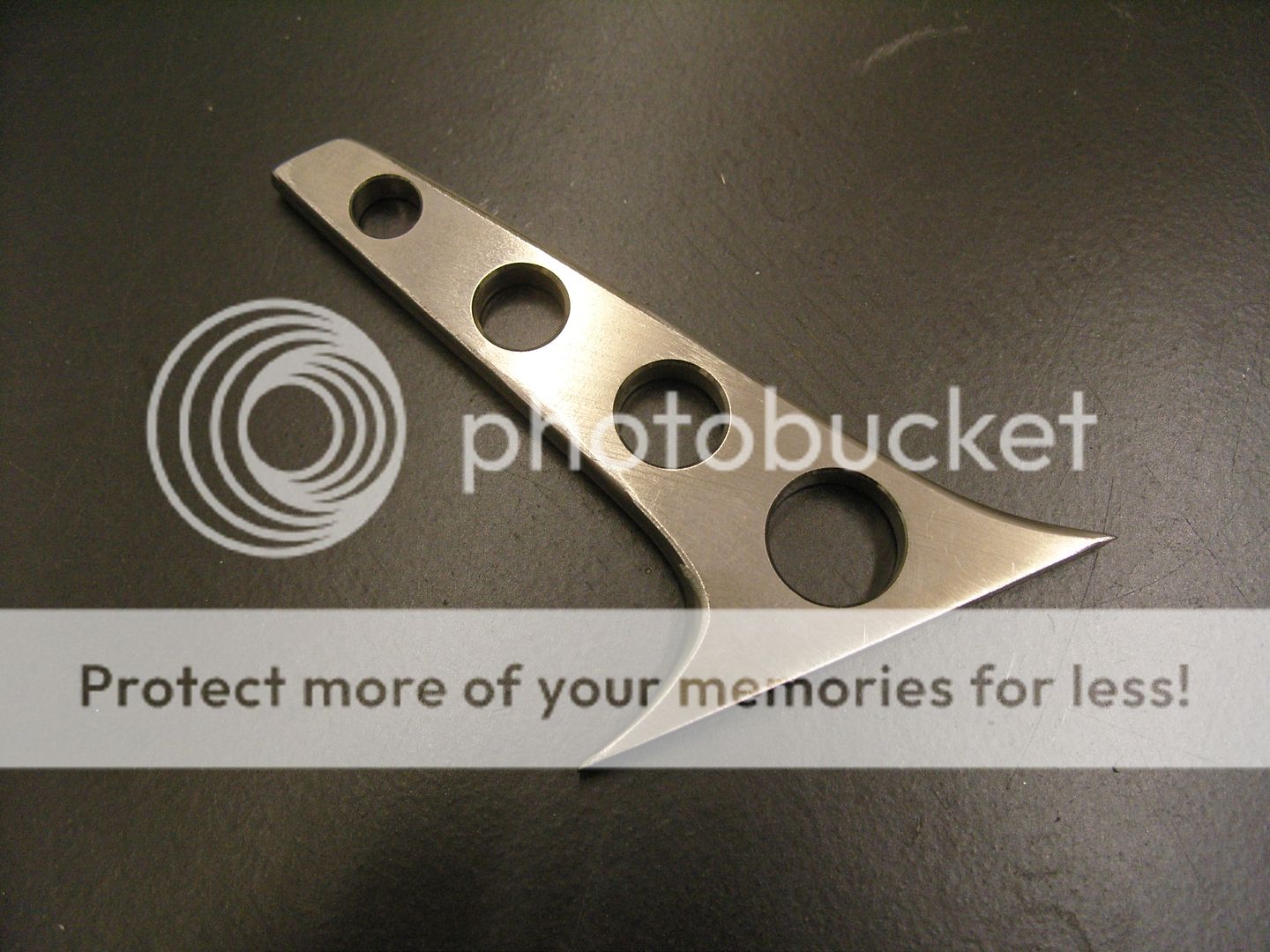
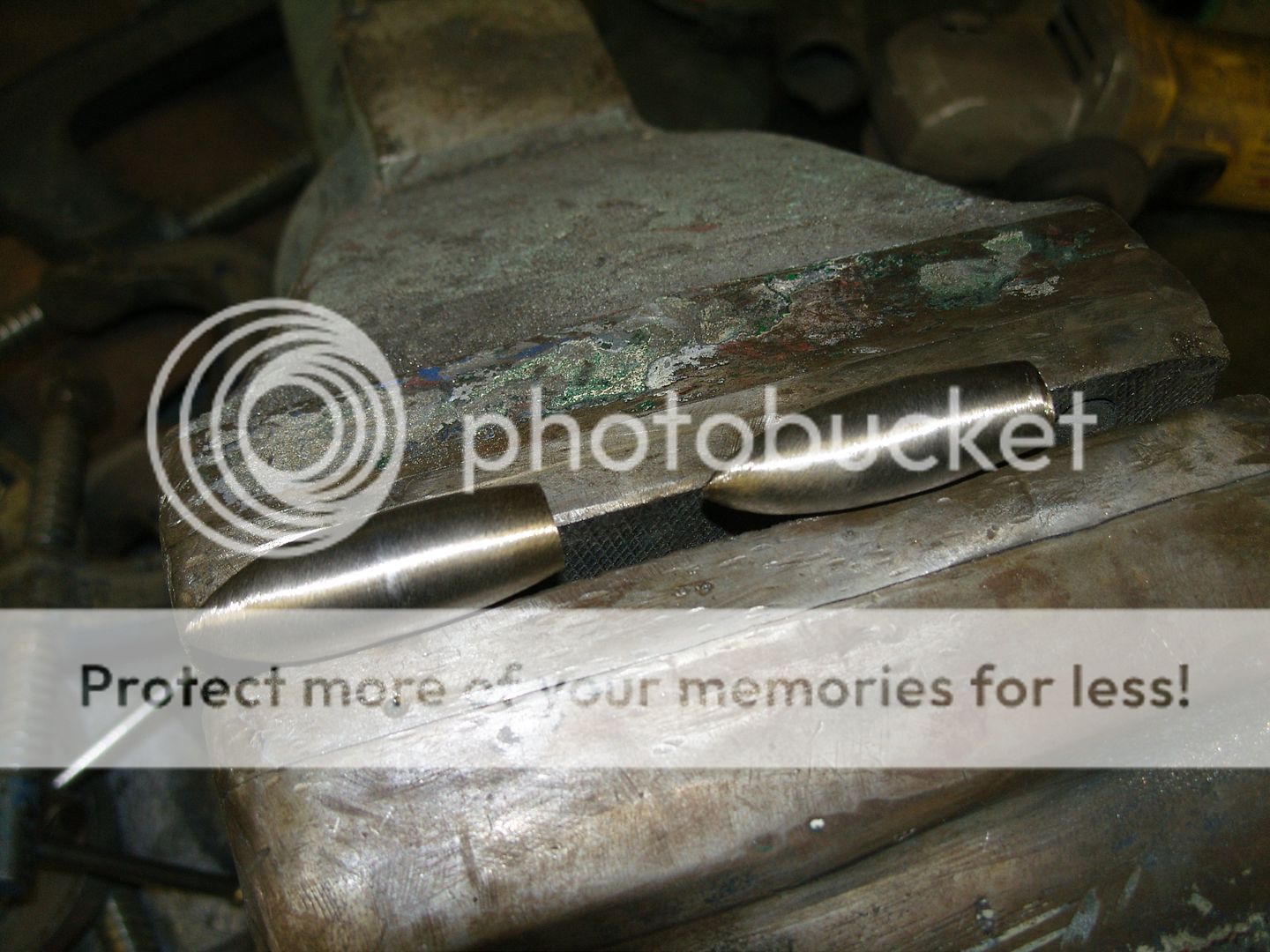
Next the edes were chamfered several times till a 50p shape was acheived, then the edges were soft sanded till smooth and radiused.
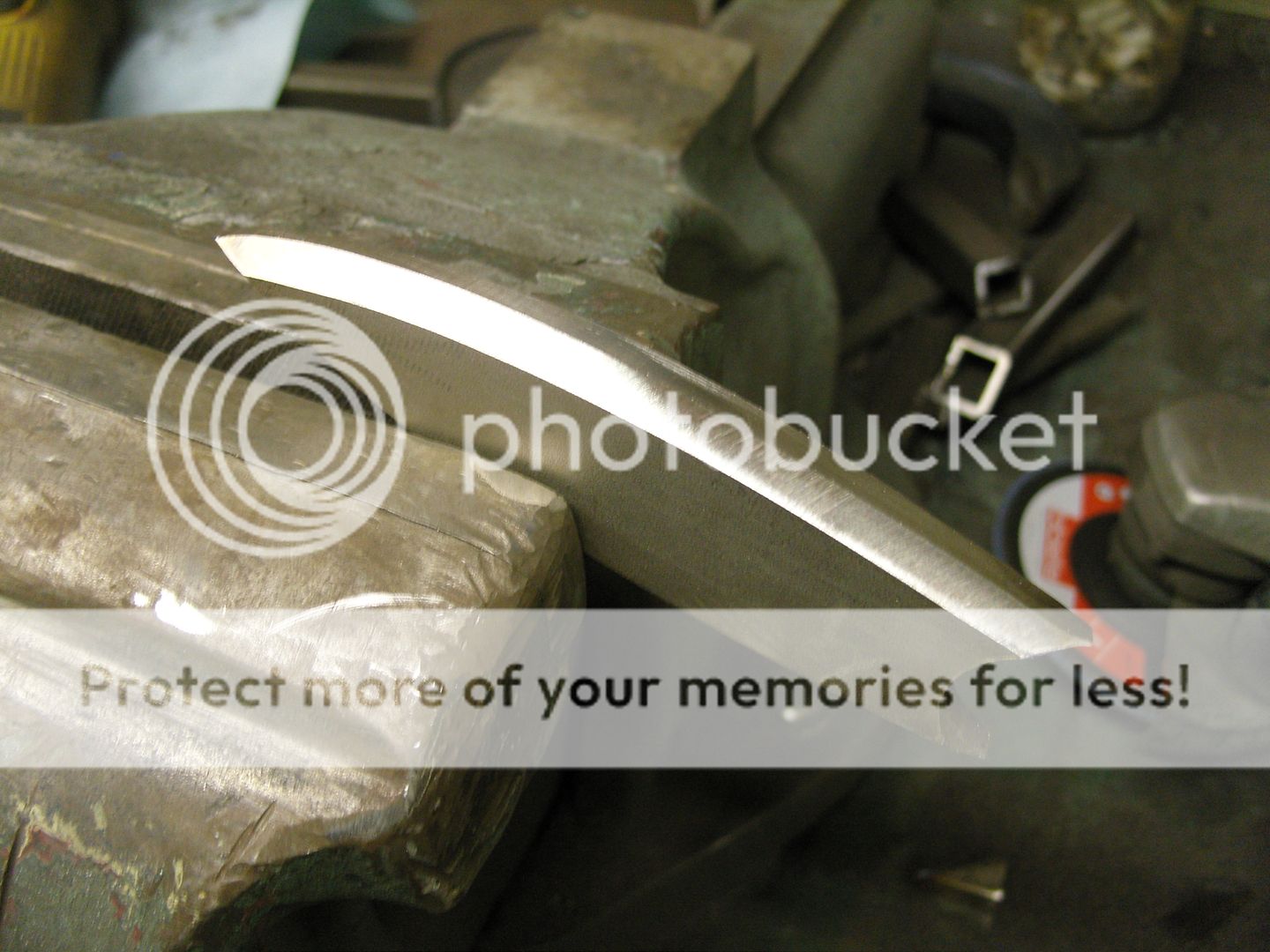
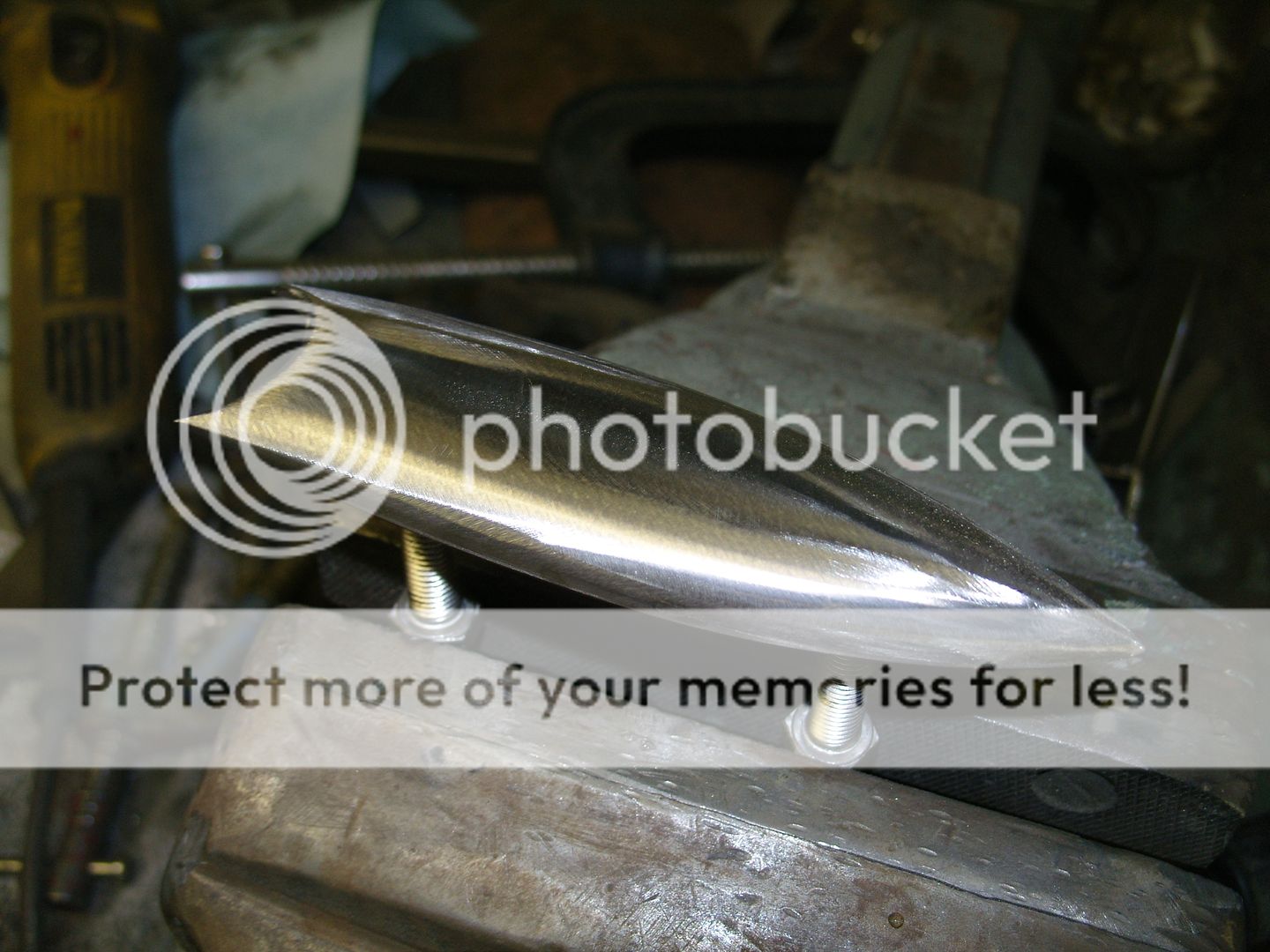
The reverse side had to be hollowed out as this sit on a swage line so again the back was ground away to suit.
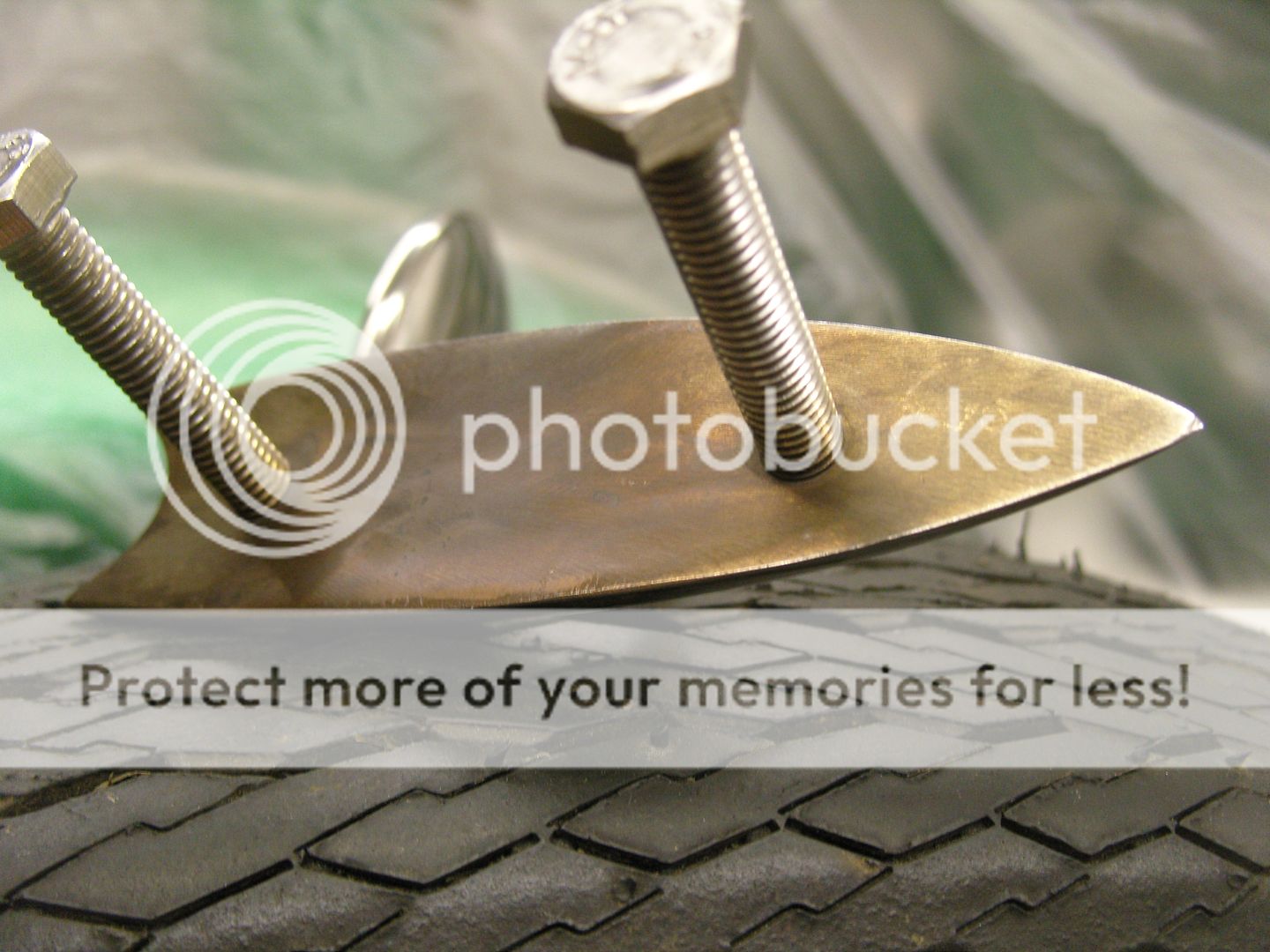
2 x 6.8mm holes were drilled and tapped 8mm for mounting studs, the long bolts are temporary and for holding during the polishing process.
All the parts were then TIG welded together, a fair bit of rod was used so i had something to get a nice radius with.
The finished Mirrors.
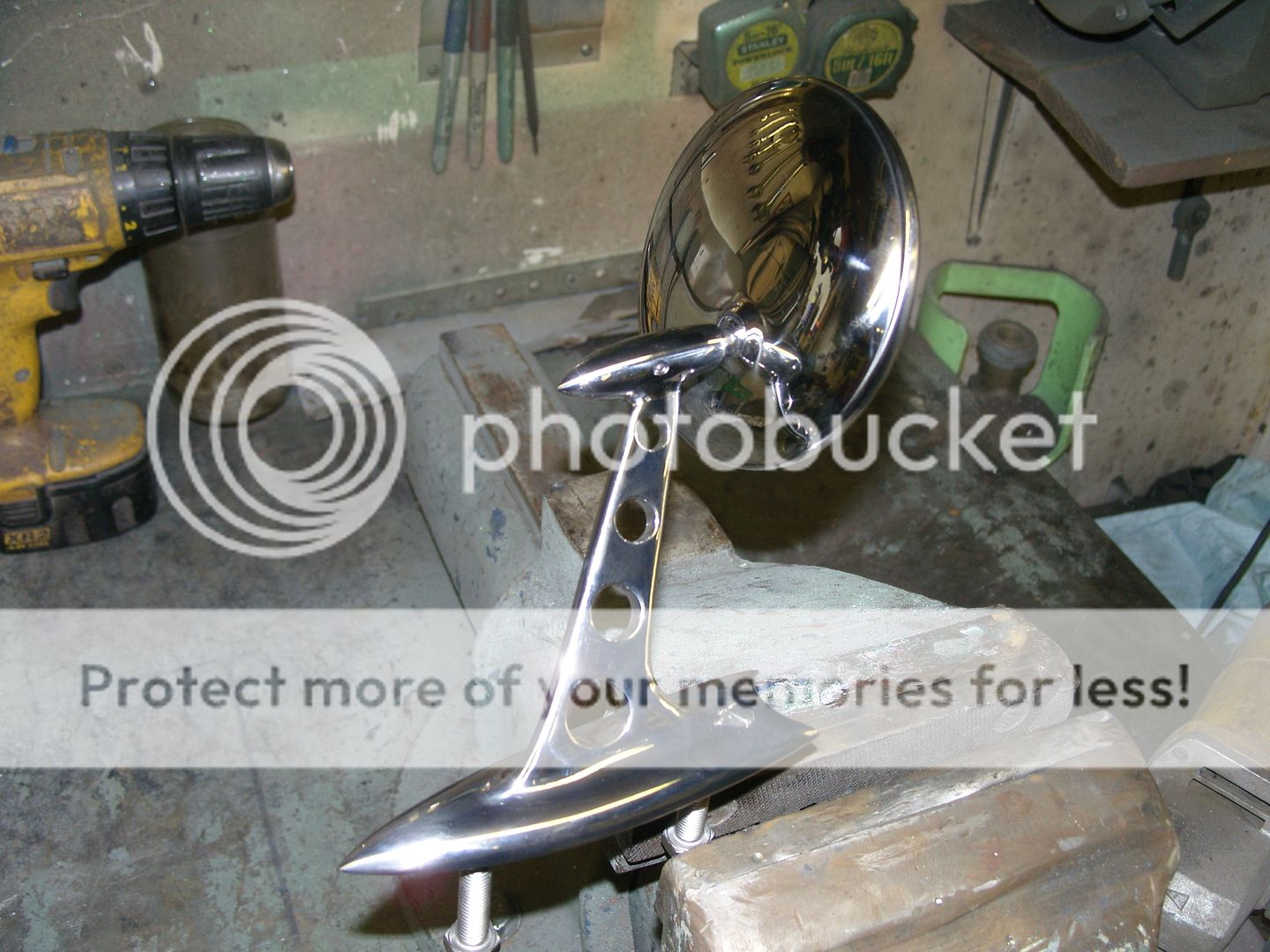
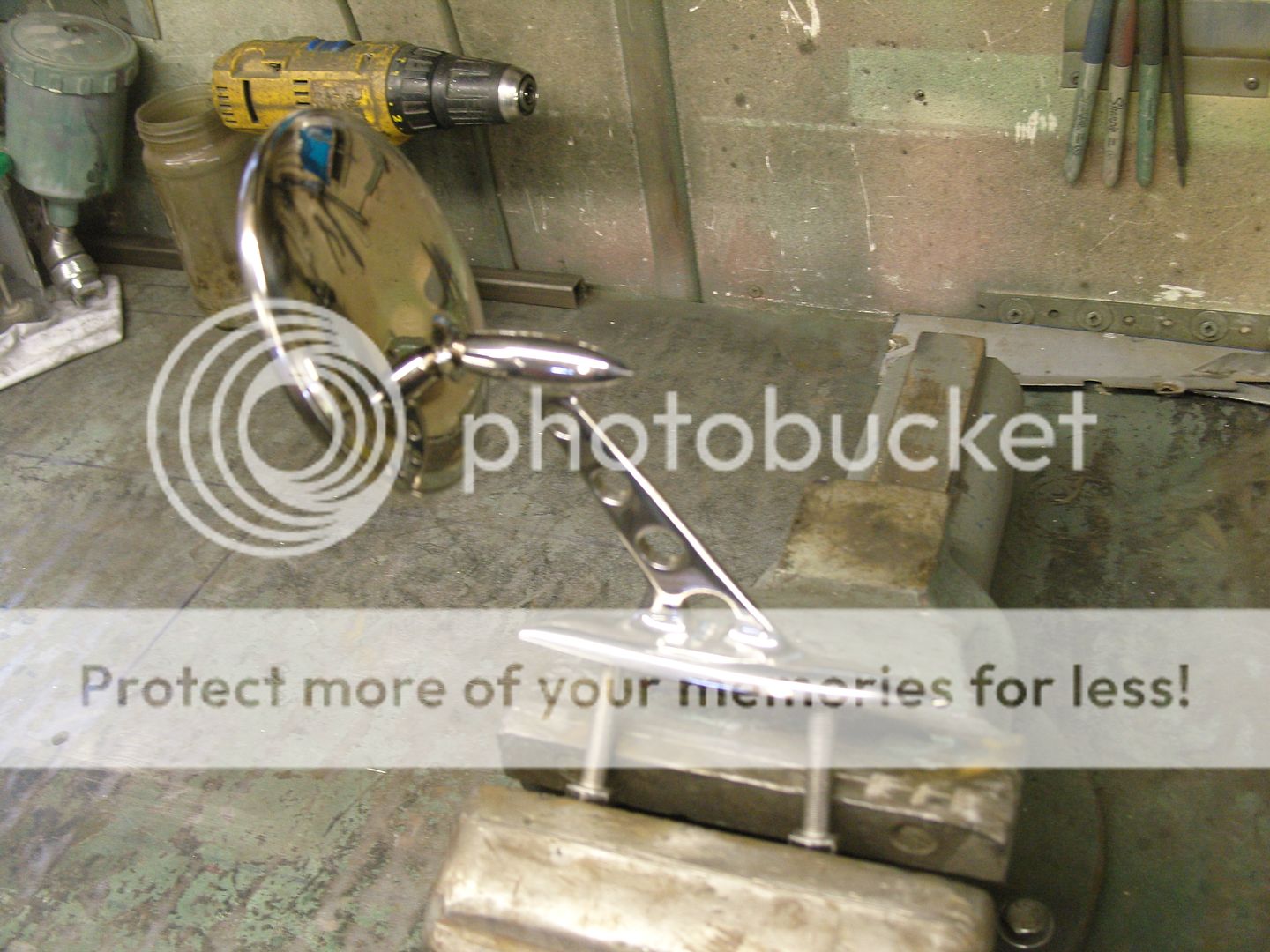
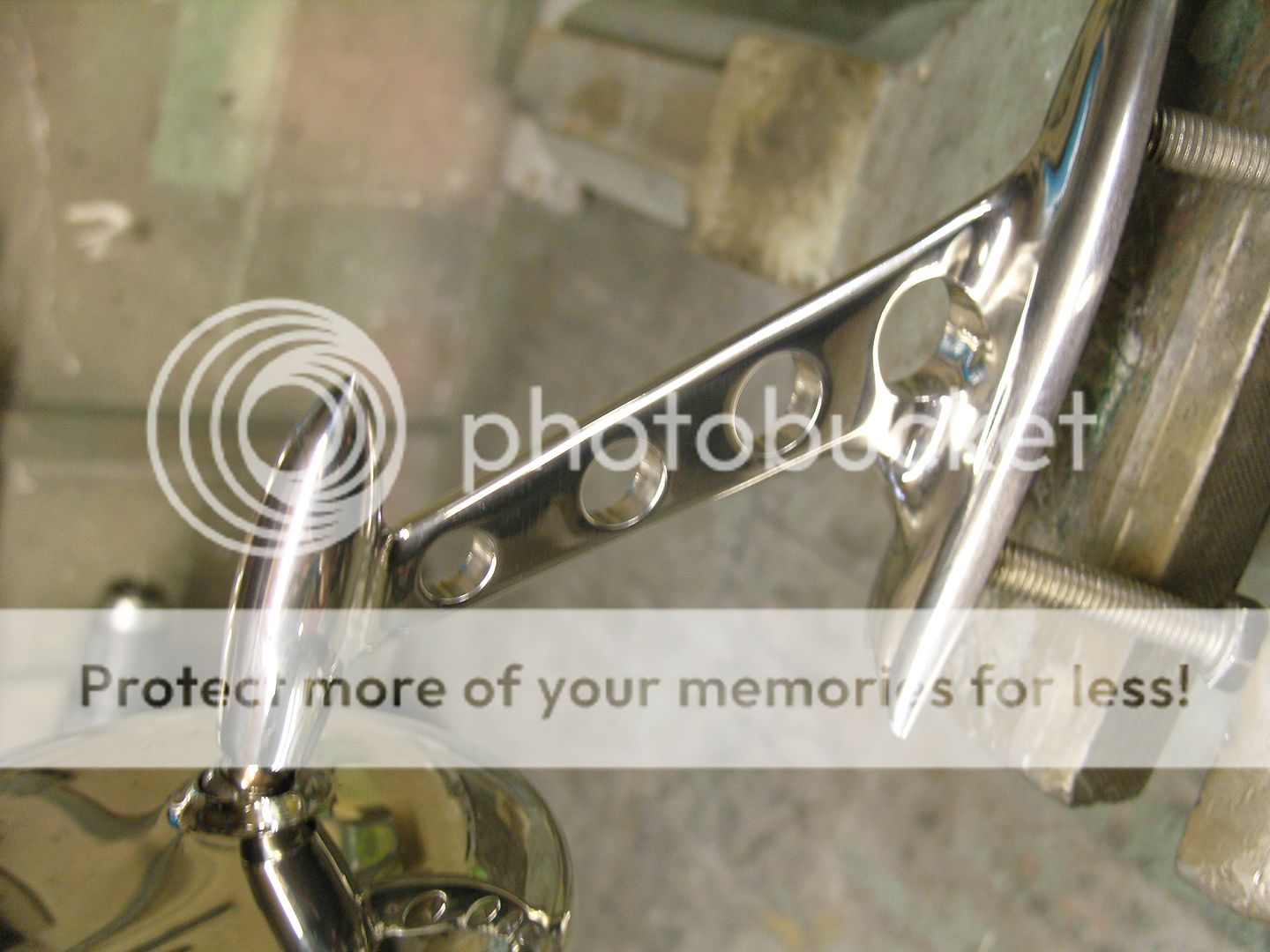
________________