Mykk
Active Member
I was thinking a while back (uh oh), my bucket really has just been a street cruiser instead of a track machine. Yet the suspension is so stiff on the street it's an absolute bear to drive for any time or distance. With the lessons learned from putting the thing together by the seat of my pants, I think I can put together a more street friendly chassis. My fabrication and welding has improved over time, perhaps it's time to consider making V1.5 of the BMW powered T-bucket with street friendly suspension in mind, applying the things I've learned putting the first one together.
However, I also have difficulty doing things by the book. So a few experimental ideas that have been rattling around in my head will be implemented too, as you'll see. There will still be plenty of "Cross that bridge when we get to it" fabrication on this one too:
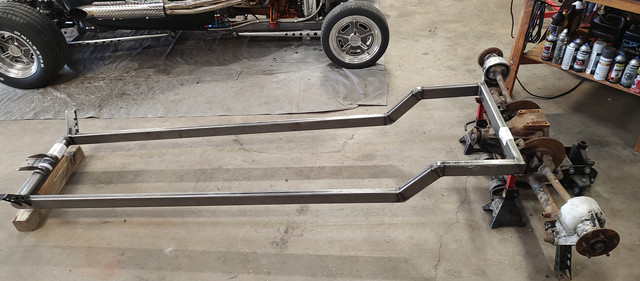
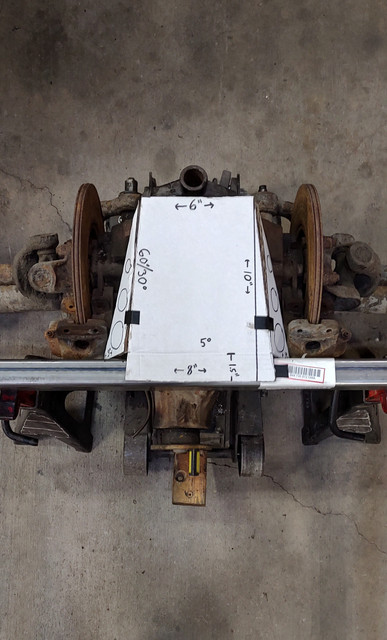
SendCutSend has already cut out and bent the rear differential perch from .250" mild steel, awaiting part arrival before welding it to the frame
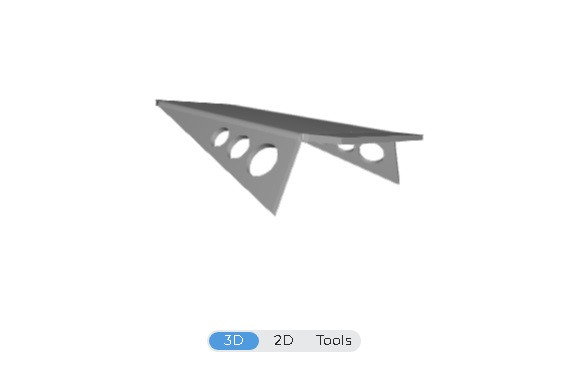
The other side of the frame from the perch will receive .250" gussets.
The rear leaf spring idea may not pan out in the long run, but I'm going to try it. Here you can see the wrong spring is bolted to the wrong plate thickness at the bottom of the Jag diff. I plan to make a .250" thick plate that bolts to the bottom of the diff and is welded to the front support mount bar not yet installed on the jag rear end. Then run the front diff supports from the cross bar up to the frame.
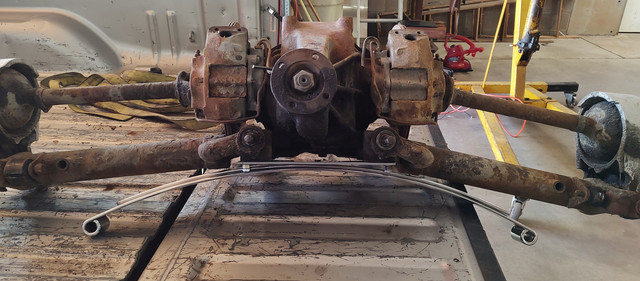
The new body arrived last night:
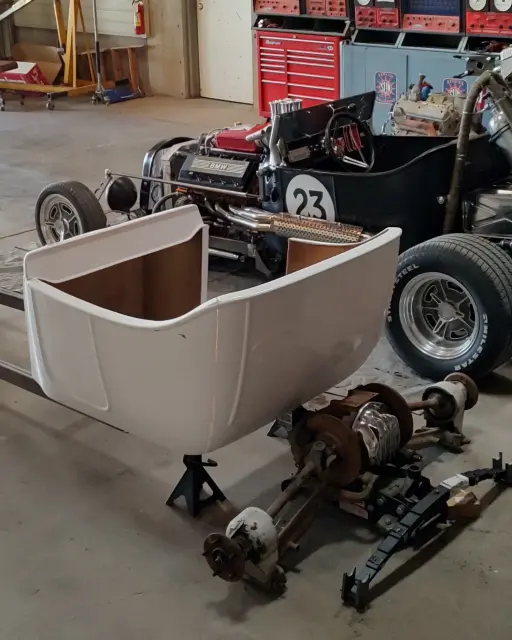
Planning to keep the kick up of the frame in the body. Mount the bench seat to the kick up, mount the electronics under the bench seat.
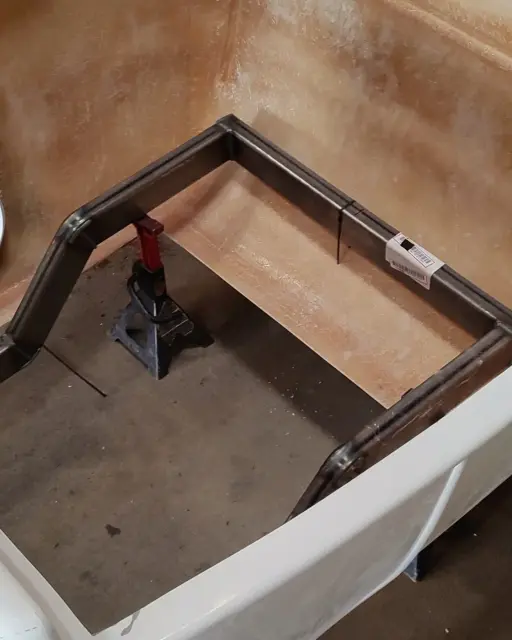
Cut the window out of the body for the frame crossmember to sneak through:
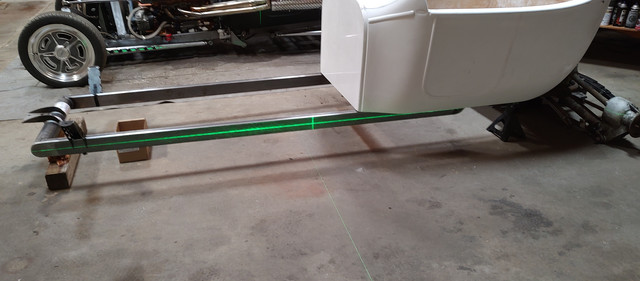
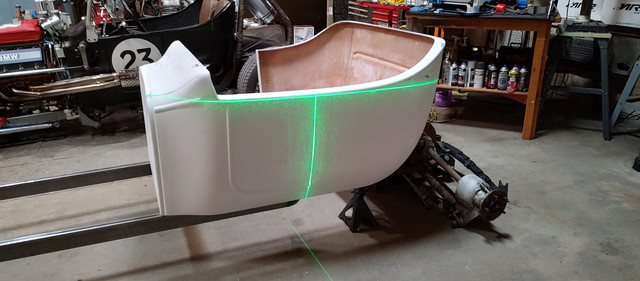
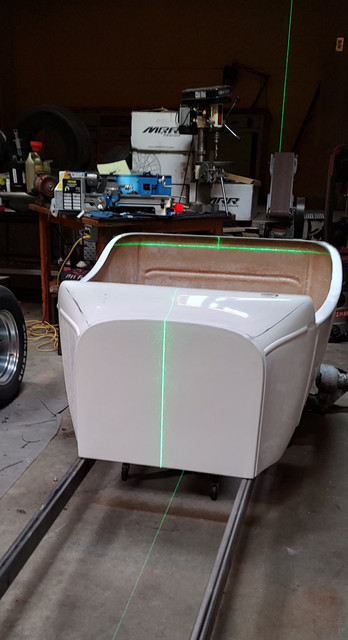
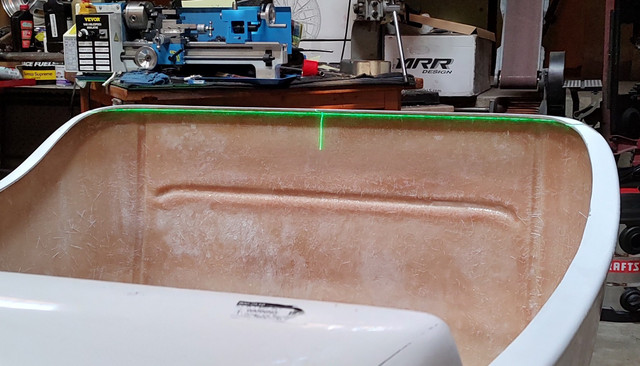
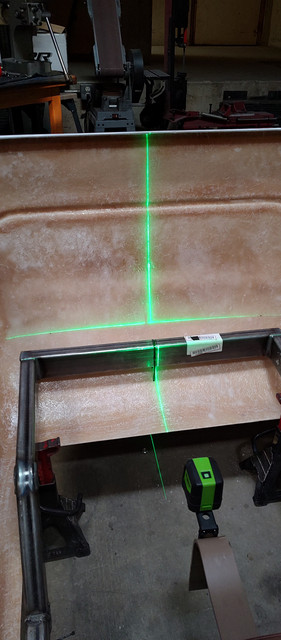
Marked the laser lines on the body above and below the frame rails and cut it out:
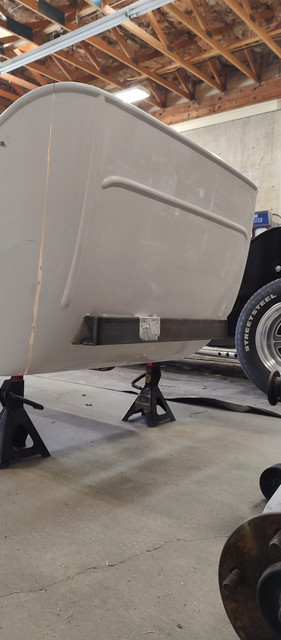
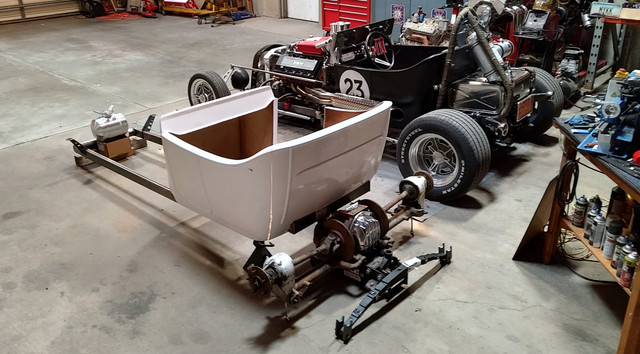
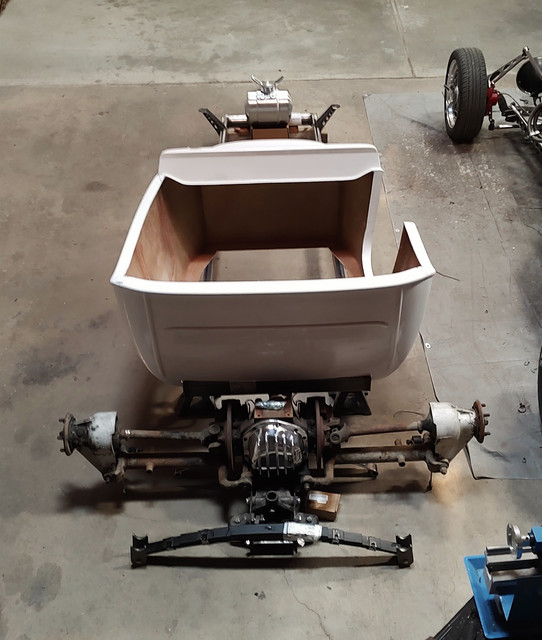
Check back for updates, thanks for checking out my next project build.
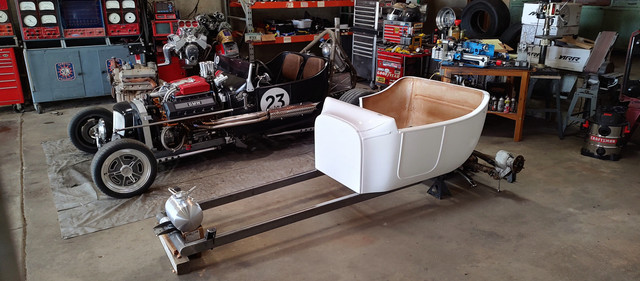
However, I also have difficulty doing things by the book. So a few experimental ideas that have been rattling around in my head will be implemented too, as you'll see. There will still be plenty of "Cross that bridge when we get to it" fabrication on this one too:
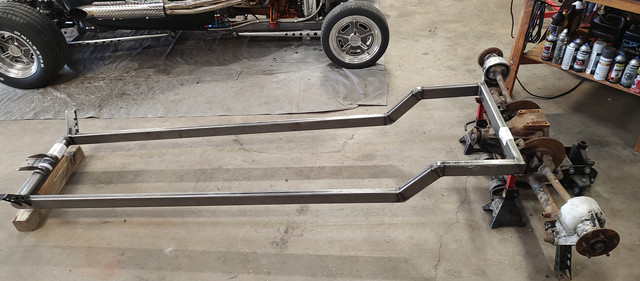
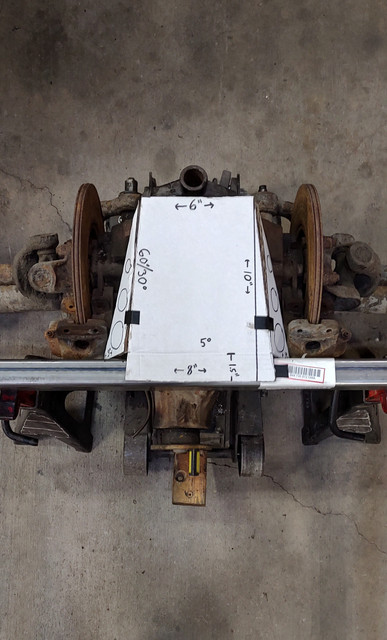
SendCutSend has already cut out and bent the rear differential perch from .250" mild steel, awaiting part arrival before welding it to the frame
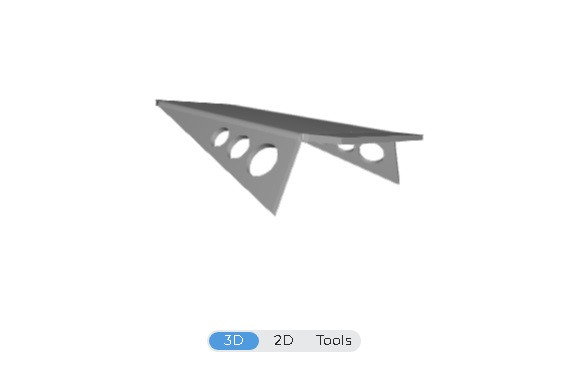
The other side of the frame from the perch will receive .250" gussets.
The rear leaf spring idea may not pan out in the long run, but I'm going to try it. Here you can see the wrong spring is bolted to the wrong plate thickness at the bottom of the Jag diff. I plan to make a .250" thick plate that bolts to the bottom of the diff and is welded to the front support mount bar not yet installed on the jag rear end. Then run the front diff supports from the cross bar up to the frame.
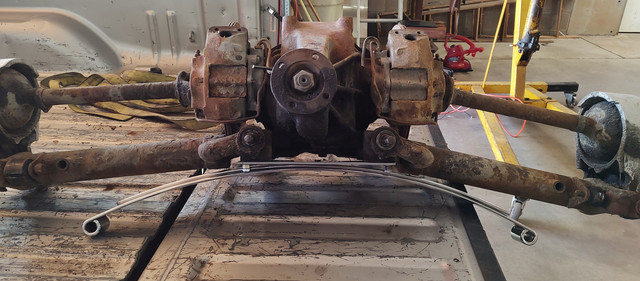
The new body arrived last night:
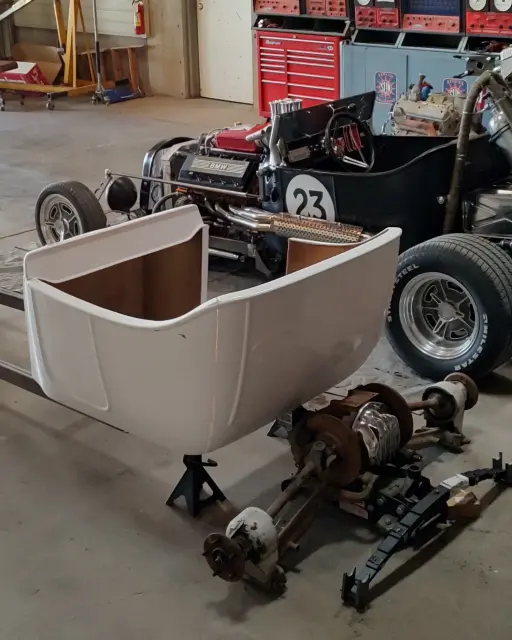
Planning to keep the kick up of the frame in the body. Mount the bench seat to the kick up, mount the electronics under the bench seat.
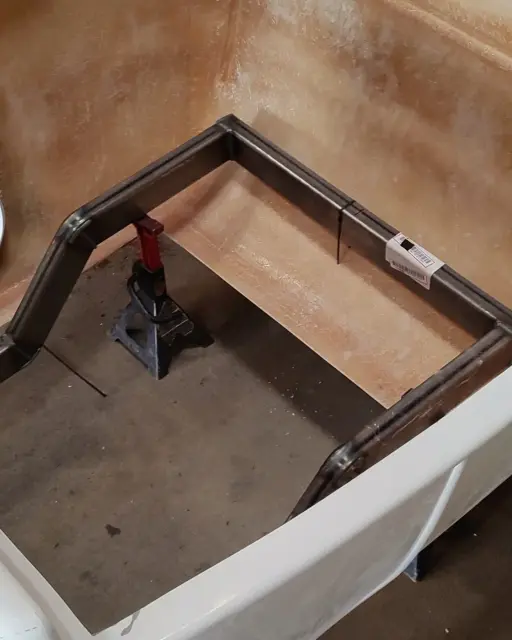
Cut the window out of the body for the frame crossmember to sneak through:
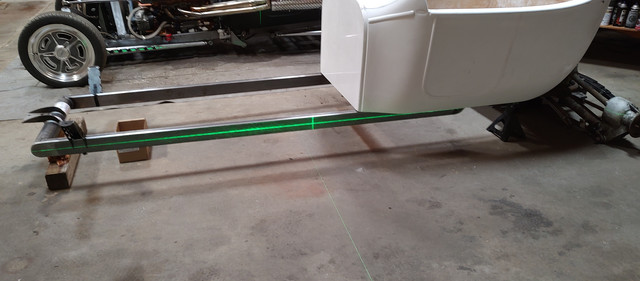
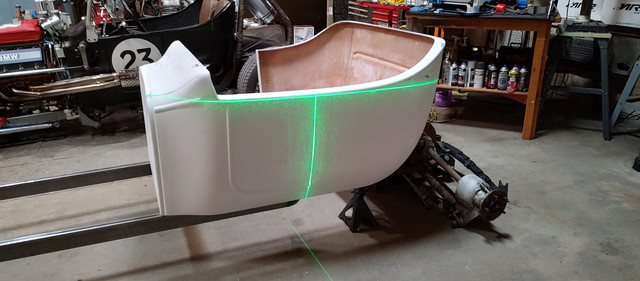
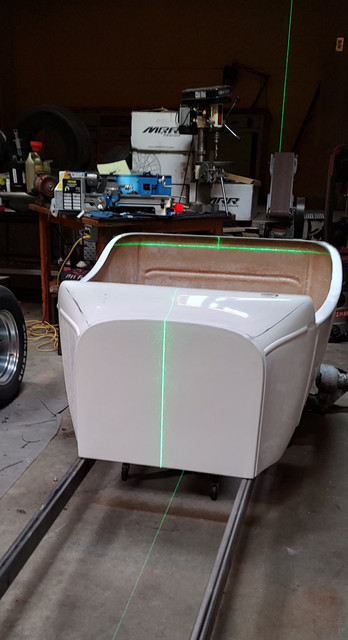
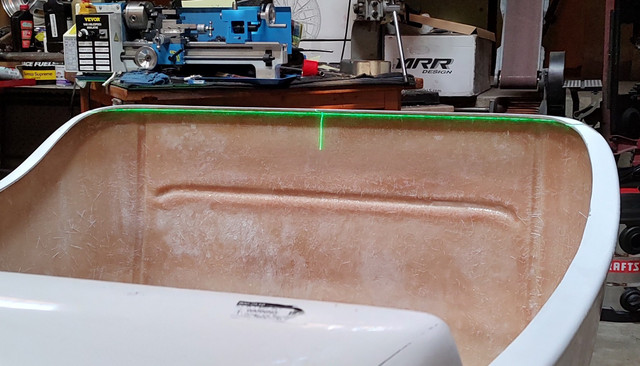
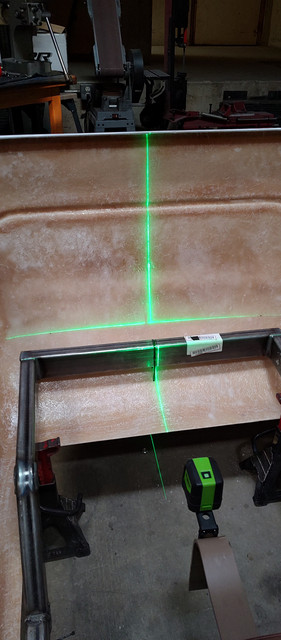
Marked the laser lines on the body above and below the frame rails and cut it out:
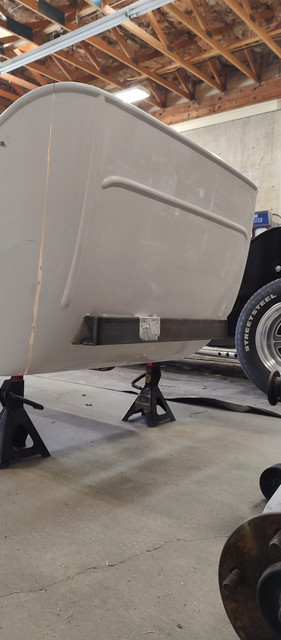
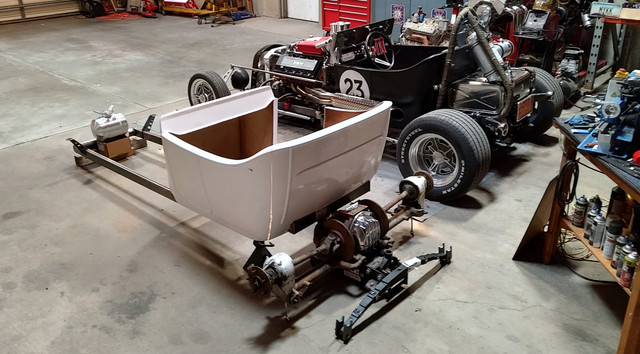
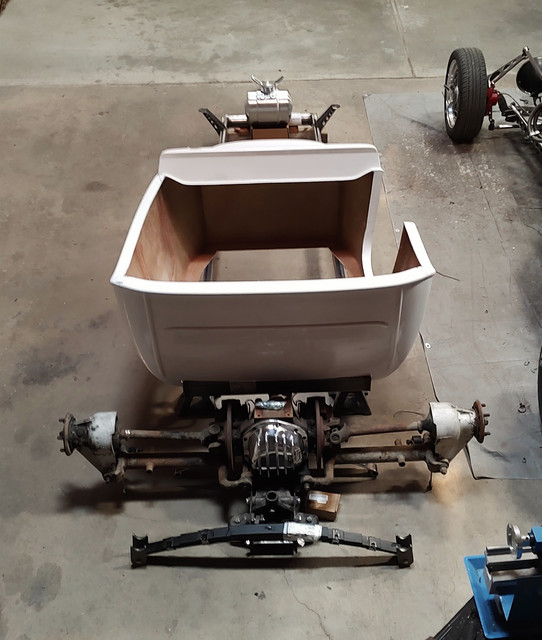
Check back for updates, thanks for checking out my next project build.
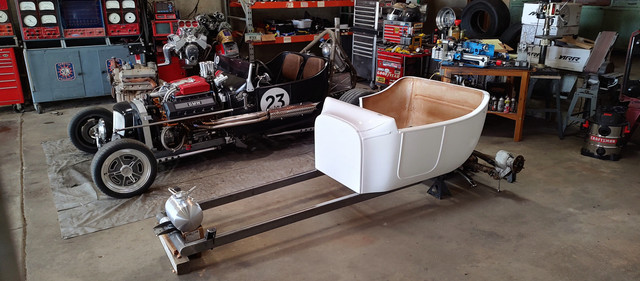