One of the projects in the shop now is a '27 roadster body that has been channeled sometime in it's history. The present owner wants to build it as a hiboy. Problem; the body sub-frame is just a memory. Solution; build a new space type sub-frame from 1"x1" square tubing. Problem; how to shape 4 identical tubes to fit the body and frame. Solution; as follows,
Basically 3, 2-3/4" steel casters, 2 mounted in fixed positions and 1 adjustable with a crank to move the tube.
By tightening the adjustable caster 1/4 turn and moving the tube back and forth, a curve starts to appear.
3 passes turned a straight tube into a curve one with a 1-1/4" bow.
The steel came from my scrap pile. The 3 casters were $12 at the farm store. About 8 hours to build including coffee breaks. I can provide a sketch to anyone interested in building their own.
Ron
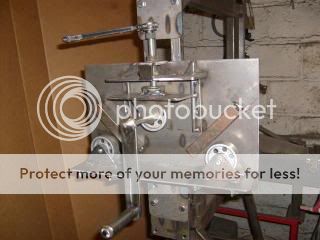
Basically 3, 2-3/4" steel casters, 2 mounted in fixed positions and 1 adjustable with a crank to move the tube.
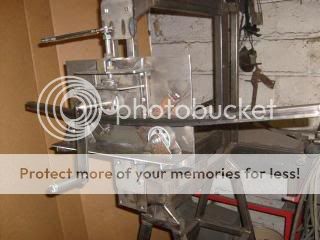
By tightening the adjustable caster 1/4 turn and moving the tube back and forth, a curve starts to appear.
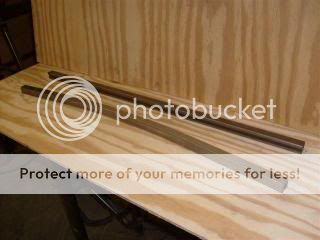
3 passes turned a straight tube into a curve one with a 1-1/4" bow.
The steel came from my scrap pile. The 3 casters were $12 at the farm store. About 8 hours to build including coffee breaks. I can provide a sketch to anyone interested in building their own.
Ron