DonnyRay
Well-Known Member
Good advice. I laid 3 layers of cloth & I used wax paper as a release agent. After what I've experienced using wax paper , I say DO NOT USE WAX PAPER. Tomorrow I'm going to add 3 or 4 layers of 1 1/2 oz fiberglass mat. I'll flip the roof over & repair the damage caused by the wax paper. Here is some photos to give you a visual of the damage. For the rest of the
glassing job i'll sand the mock windshield ; apply some white enamel paint & use car wax instead of wax paper.
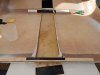
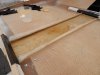
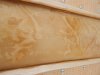