Chris@whiterhino
New Member
Ok for 8 years or so I have been DIEING for an English Wheel. I've draw up CAD files of them and changed it here and there etc. Well today I happened to be at Oneal Steel and they had a 4' x 47" drop of 5/16 plate. So I got it at scrap prices and only paid $80.00 for it, WOW!!
Anyway, so I start cutting the main part of teh E Wheel out.
Here are a couple others when its done.
layed out on the floor.
This is 4' x 4', ok ok more like 47" x 47". Now that I have that and the 1/4" x 2" x 2" Steel tube all I need to do is weld it up and order my dies.
I'll keep this updated.
I had a friend come help me load it on the table and while we were loading it there was a small booboo....
Thats a 1.5" gash in my hand.
I had my friend handle the camer because I could pinch the skin and you can see everything in here. I thought it was kinda cool, Angela however does not.
Anyway, so I start cutting the main part of teh E Wheel out.
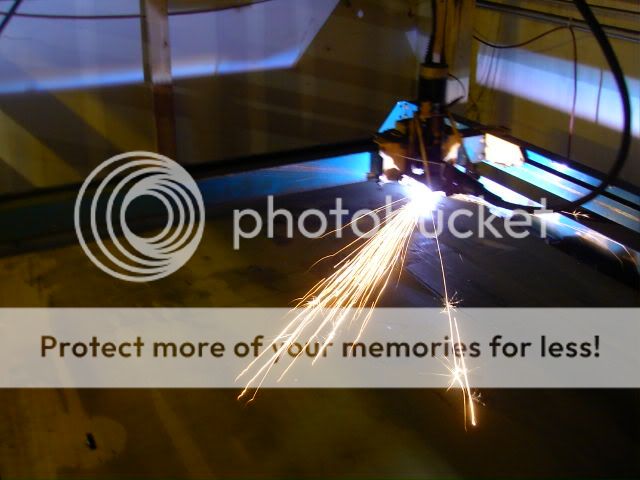
Here are a couple others when its done.
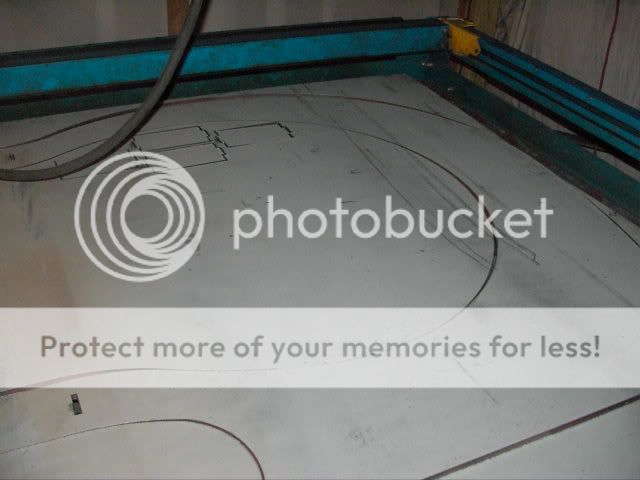
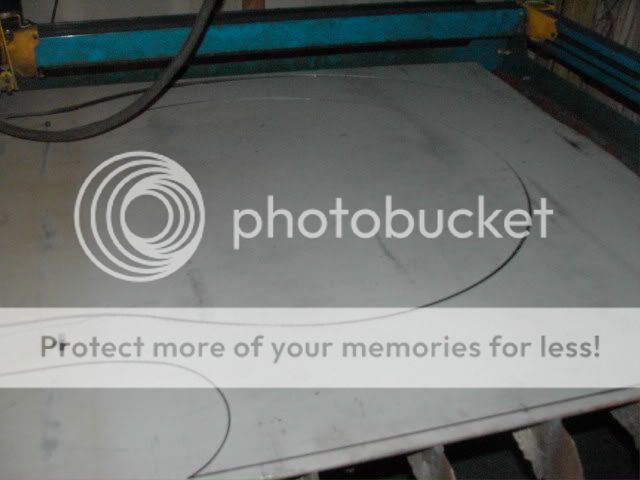
layed out on the floor.
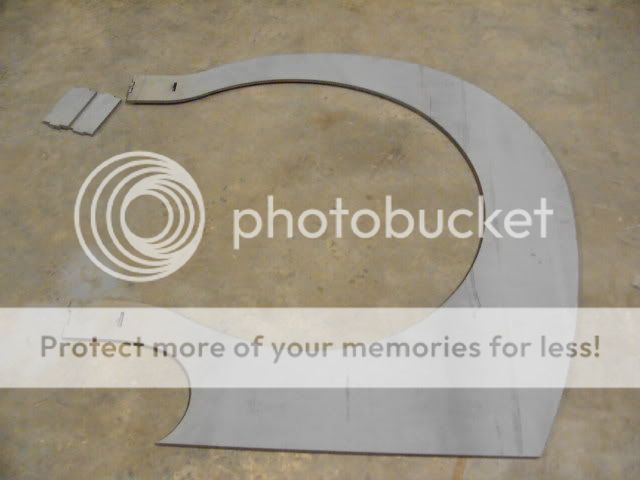
This is 4' x 4', ok ok more like 47" x 47". Now that I have that and the 1/4" x 2" x 2" Steel tube all I need to do is weld it up and order my dies.
I'll keep this updated.
I had a friend come help me load it on the table and while we were loading it there was a small booboo....
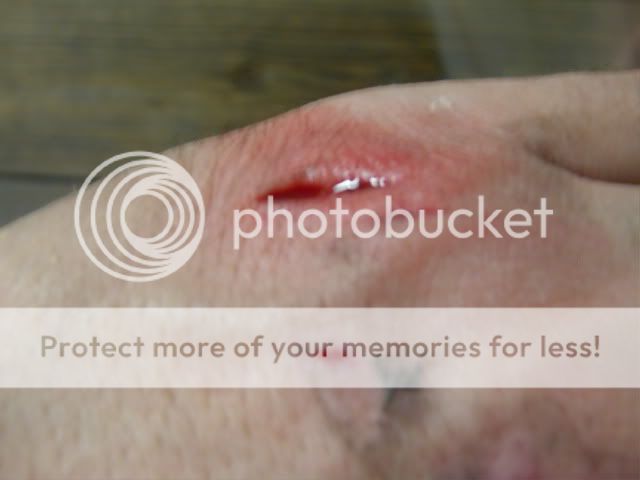
Thats a 1.5" gash in my hand.
I had my friend handle the camer because I could pinch the skin and you can see everything in here. I thought it was kinda cool, Angela however does not.
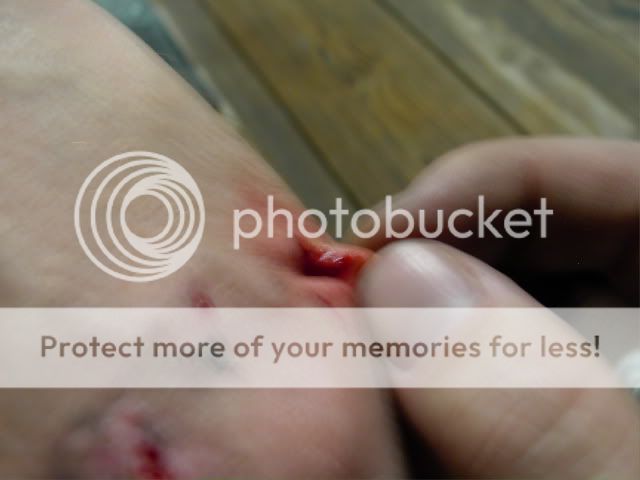