fletcherson
Well-Known Member
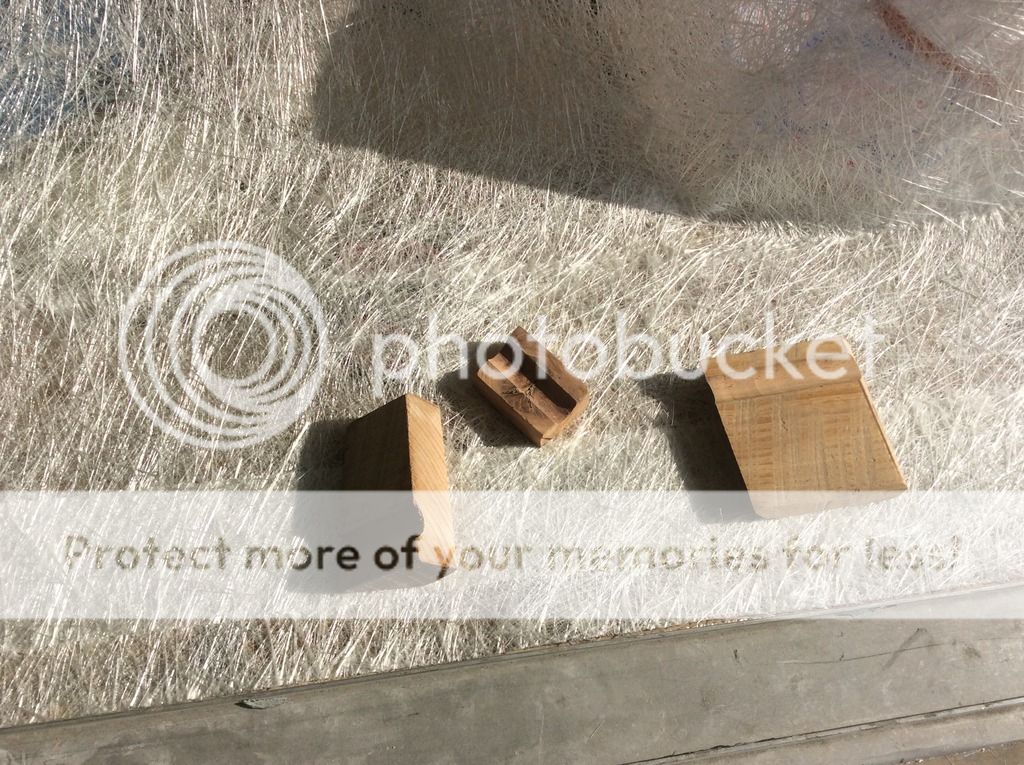
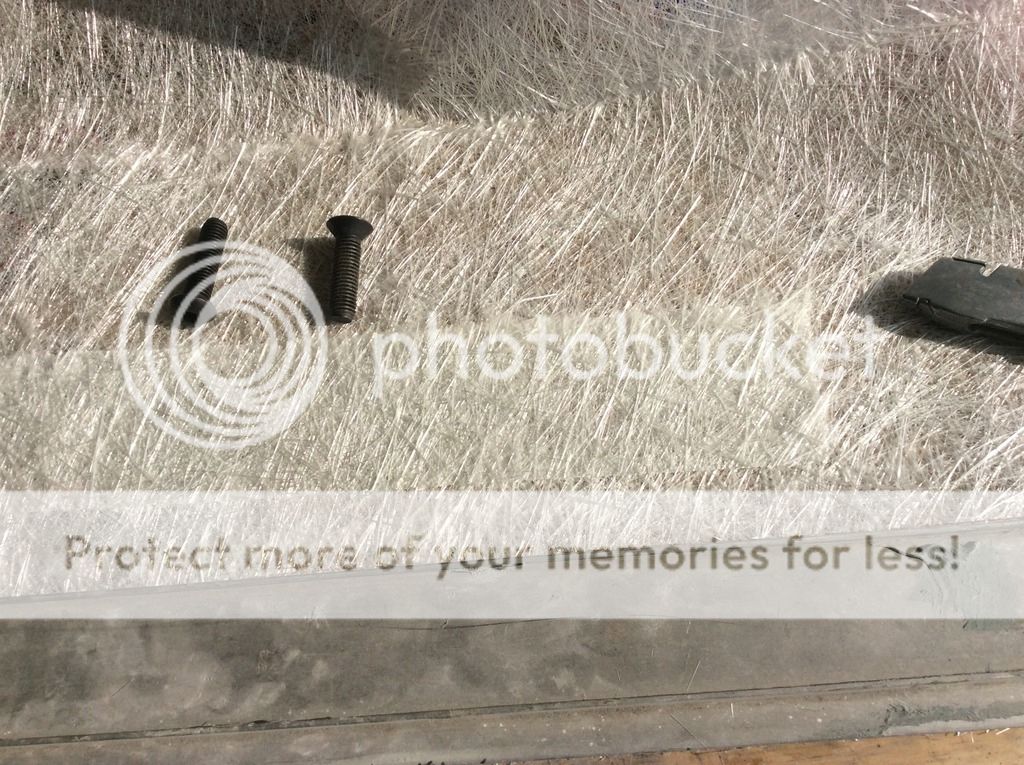
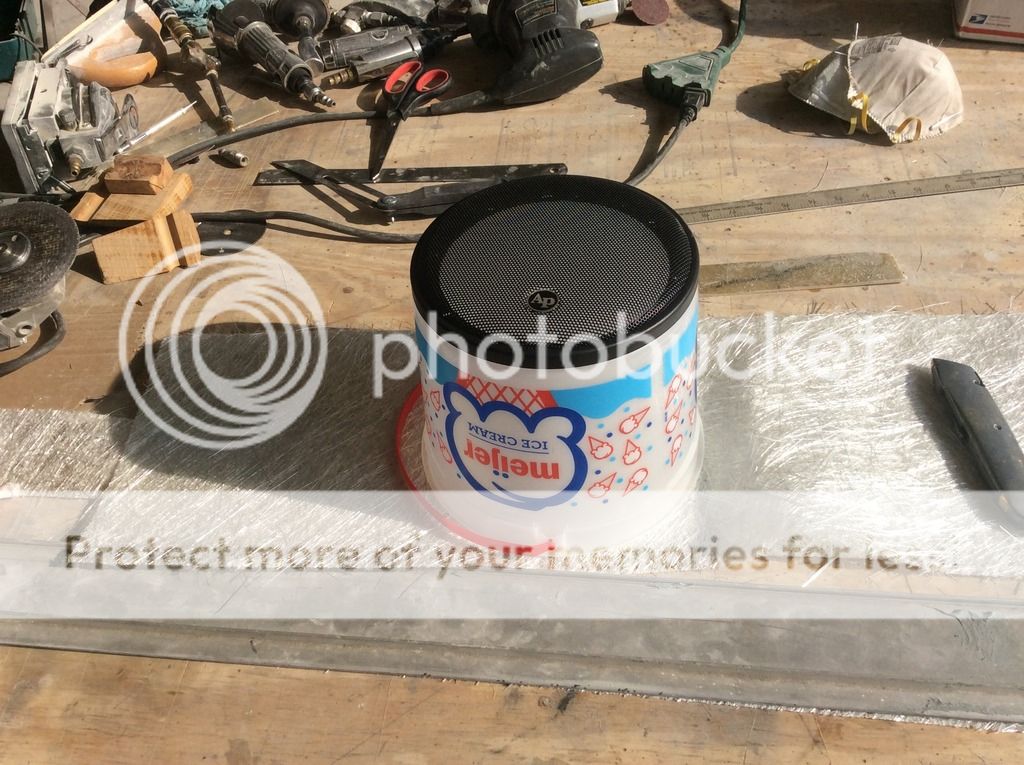
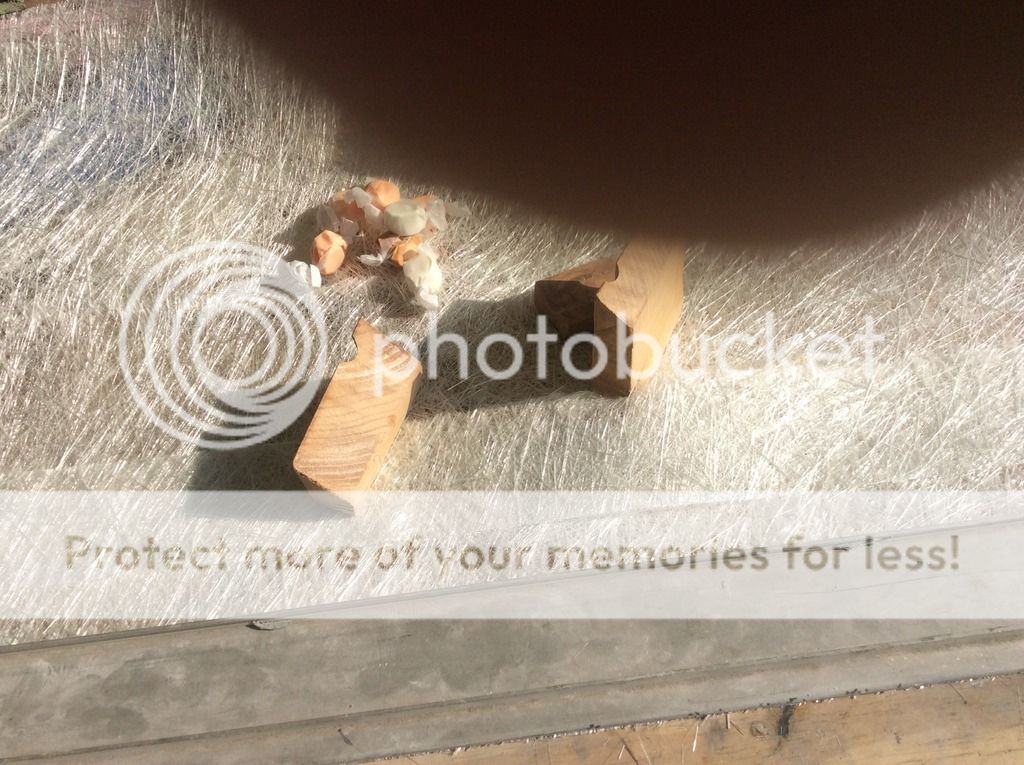
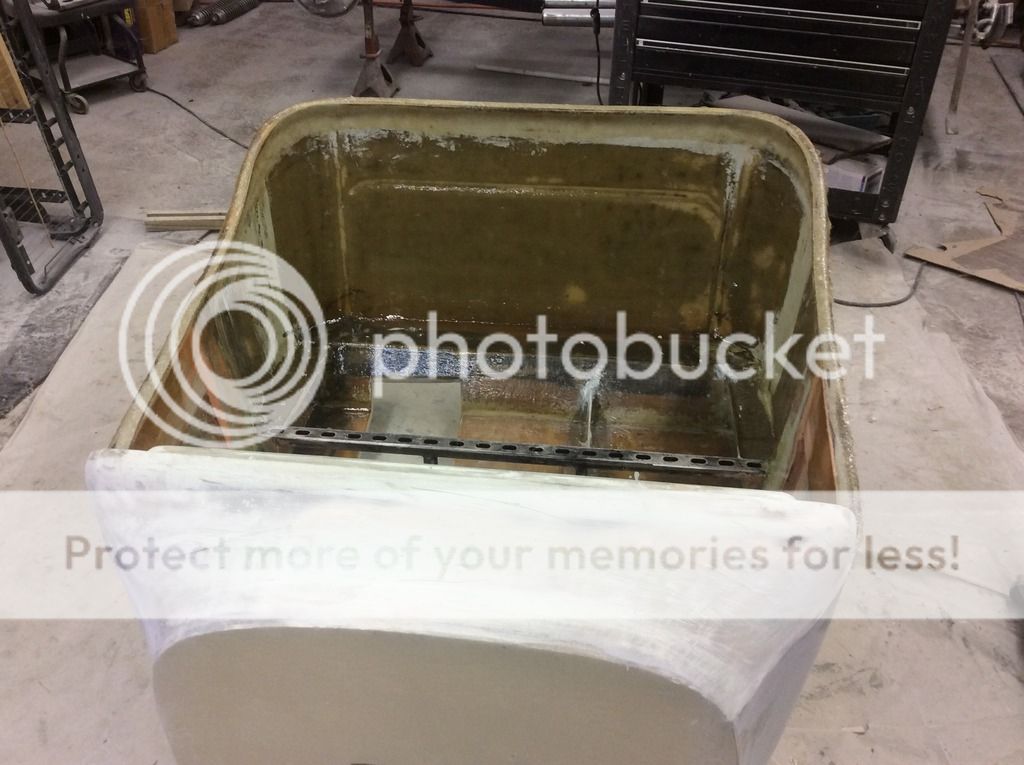
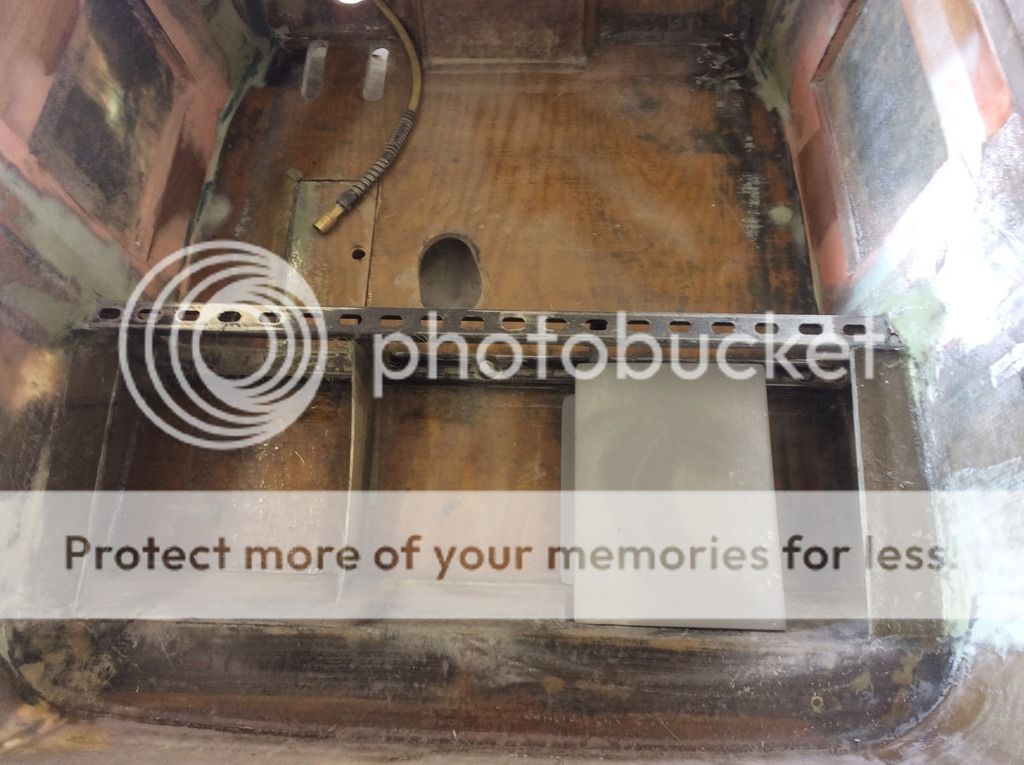
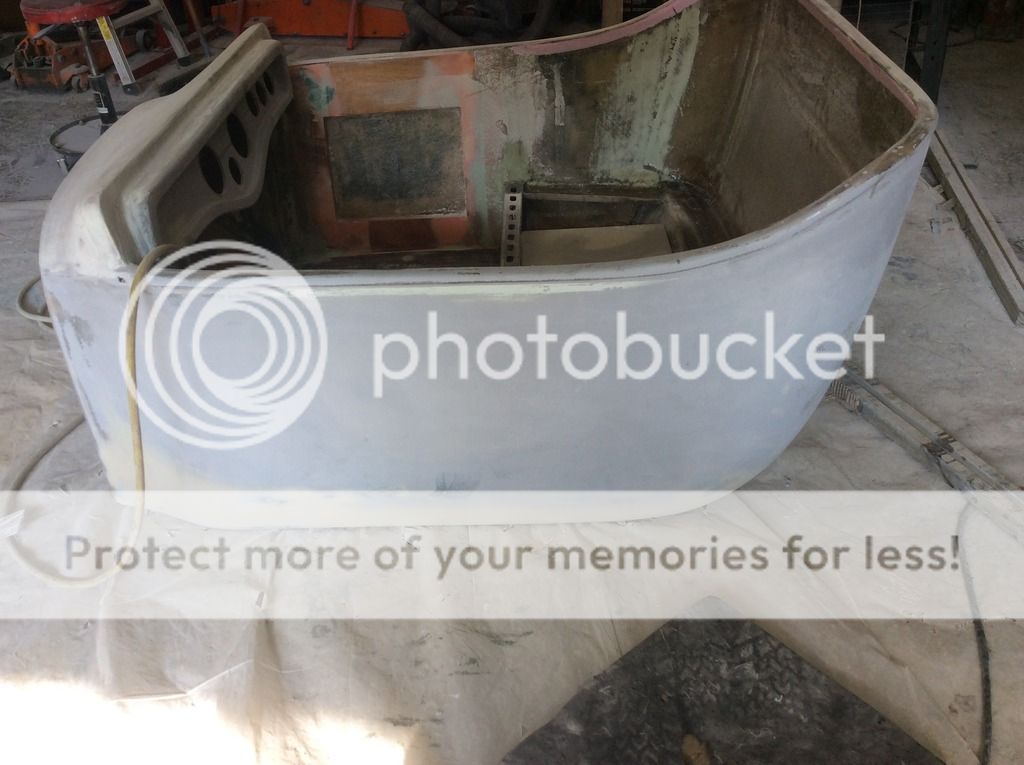
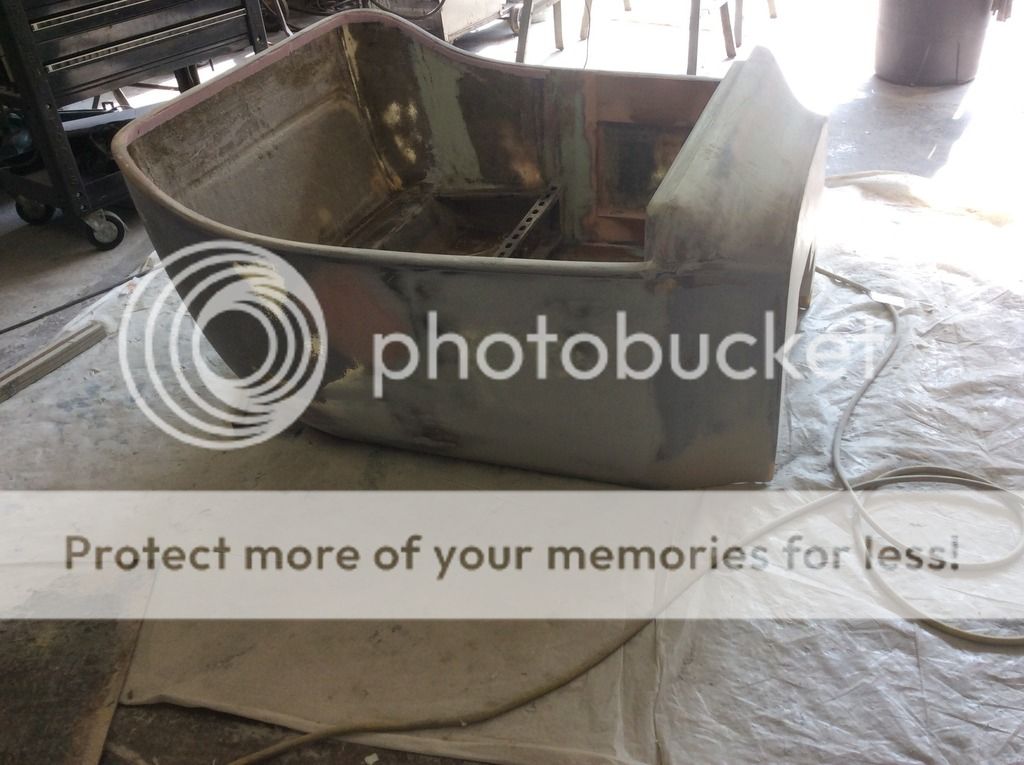
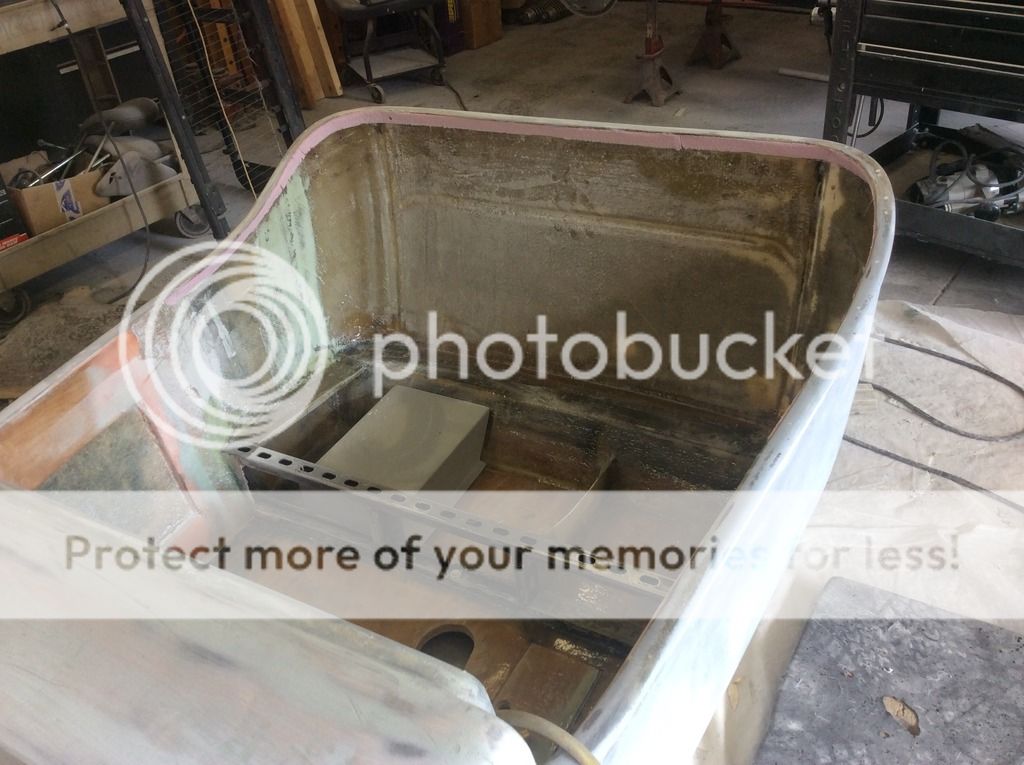
That sounds like some handy stuff! I'm going to get some just to have on hand.There is a thing called polymorph. Its beads of plastic that go soft when put into boiling water and then cools to a hard plastic. I used it to form a sanding profile on a bit of swage line that was correct and then after cooling it became the backing block for the rest of the contour lines on the body. Its only about 10 bucks for a pack and can be remelted and reformed again and again. Saves on wood and routing.
Have a look on UTub for ideas. I have found a few uses for it besides the above. It can be file'd, drilled and tapped once hard. Useful stuff to have around.
G
Bill, I didn't realize that your passenger door was already cut. That's going to prove to be challenging to reinforce enough to cut both sides. Without channeling, it seems difficult to build rockers or the like. You could reinforce the actual floor, but you will be asking a lot of the bond between the body and floor to provide enough strength. Even with a well reinforced floor, I think bracing fore and aft of both doors are manidtory to provide enough rigidity to allow the body to retain its shape to allow the doors to function properly. Of cource, I'm not looking at your project, but I'd look real hard at possibly channeling it enough to build in some rockers and reinforcements. I understand your accessibility issues, but you need some strength for the body to support the doors. Just wondering why not channel it? It won't interfere with its ability to lower, unless you channel it deeper than the frame height. What am I missing?I wish I could get by with a single door, but the existing passenger door is not large enough, and trying to slide across and get my legs over the transmission tunnel would be impossible.
Bill, I didn't realize that your passenger door was already cut. That's going to prove to be challenging to reinforce enough to cut both sides. Without channeling, it seems difficult to build rockers or the like. You could reinforce the actual floor, but you will be asking a lot of the bond between the body and floor to provide enough strength. Even with a well reinforced floor, I think bracing fore and aft of both doors are manidtory to provide enough rigidity to allow the body to retain its shape to allow the doors to function properly. Of cource, I'm not looking at your project, but I'd look real hard at possibly channeling it enough to build in some rockers and reinforcements. I understand your accessibility issues, but you need some strength for the body to support the doors. Just wondering why not channel it? It won't interfere with its ability to lower, unless you channel it deeper than the frame height. What am I missing?
Being pre butchered takes the anx out of making it how you want it. Glass is very repairable, changeable, it just takes some work and a supply of material. If you bond your mounts to the body and they bolt to the frame, the lateral should be ok, so long as the brace is kicked off, ie the top rail in the riser so it forms a box or a gusset, etc... Here's a thought, if you don't want to channel it due to the side height, what about extending the sides below the doors to give it a channeled effect? That would allow you to box the rockers and add supports. A gallon of resin and some fabric, along with whatever you choose to add for support, the strut that I used isnt expensive and can be bought at lowes, etc... Just a thought. You have some challenges, for sure. My biggest concern for mine and yours is the cowl with the windshield and the doors and the steering column, etc all depending on one set of frame mounts and the floor to support it isn't realistic. IMHO. Think of the force that will be exerted. That's why I went to the trouble to reinforce mine as much as I did.First off I want to say that the body I have is weird and butchered. The cowl is more or less standard width, but has been stretched about 7". From the dash back the body flairs to about 4" wider and an inch longer than stock. The passenger side door that was molded into the body is about 5" longer than "standard". It appears that the body was originally made with a full floor, but for most of the floor length, a 28" wide strip has been cut out of the center. That cut out continues about halfway up the back of the body. On both the door jamb and the door itself, the lip on the bottom has been cut off. The firewall has been crudely cut for channeling. It has also been cut out for a bell housing the size of an old semi. All the cuts look like they were done by a blind man with a remote control saw, with a bad connection, from 2 states away. Yes, I got ripped off. But I have to play the cards I've been dealt.
Here is a pic of the body when it first arrived
View attachment 12198
The reason for trying to avoid channeling the body is a bit embarrassing. Besides being fat, I'm also misproportioned vertically. Standing up I'm around 5'7"...sitting down I'm taller than someone 6'2". If I were to channel the body I'd feel more on it than in it.
I think I have supporting the floor and body vertically and fore-n-aft pretty well covered. The remnants of a full floor leave a much larger bonding surface for the new floor than would be left by a typical lip. Besides bonding the floor to the body, I plan on a series of truss headed barrel nuts and Chicago bolts sandwiching the body between an aluminum strap and the floor.
Well nuts and bolts will sandwich the floor between the frame and another aluminum strap. At least 2 outriggers will support the body and floor outside the frame rails, and 2 crossmembers will support the floor inside the frame rails.
The cowl will be supported by a 1.5" OD tubing hoop that will support the steering column and the door hinges. The rear of the body will gave additional support about half way up with mounts at the top of each Kickup.
My main support concern is lateral at the rear of the door openings...but then what do I know <shrug>
Being pre butchered takes the anx out of making it how you want it. Glass is very repairable, changeable, it just takes some work and a supply of material. If you bond your mounts to the body and they bolt to the frame, the lateral should be ok, so long as the brace is kicked off, ie the top rail in the riser so it forms a box or a gusset, etc... Here's a thought, if you don't want to channel it due to the side height, what about extending the sides below the doors to give it a channeled effect? That would allow you to box the rockers and add supports. A gallon of resin and some fabric, along with whatever you choose to add for support, the strut that I used isnt expensive and can be bought at lowes, etc... Just a thought. You have some challenges, for sure. My biggest concern for mine and yours is the cowl with the windshield and the doors and the steering column, etc all depending on one set of frame mounts and the floor to support it isn't realistic. IMHO. Think of the force that will be exerted. That's why I went to the trouble to reinforce mine as much as I did.
I like your comment about having to play the cards you have been delt. Yeah you could whine about it but the attitude you have is much more constructive . Kudos...First off I want to say that the body I have is weird and butchered. The cowl is more or less standard width, but has been stretched about 7". From the dash back the body flairs to about 4" wider and an inch longer than stock. The passenger side door that was molded into the body is about 5" longer than "standard". It appears that the body was originally made with a full floor, but for most of the floor length, a 28" wide strip has been cut out of the center. That cut out continues about halfway up the back of the body. On both the door jamb and the door itself, the lip on the bottom has been cut off. The firewall has been crudely cut for channeling. It has also been cut out for a bell housing the size of an old semi. All the cuts look like they were done by a blind man with a remote control saw, with a bad connection, from 2 states away. Yes, I got ripped off. But I have to play the cards I've been dealt.
Here is a pic of the body when it first arrived
View attachment 12198
The reason for trying to avoid channeling the body is a bit embarrassing. Besides being fat, I'm also misproportioned vertically. Standing up I'm around 5'7"...sitting down I'm taller than someone 6'2". If I were to channel the body I'd feel more on it than in it.
I think I have supporting the floor and body vertically and fore-n-aft pretty well covered. The remnants of a full floor leave a much larger bonding surface for the new floor than would be left by a typical lip. Besides bonding the floor to the body, I plan on a series of truss headed barrel nuts and Chicago bolts sandwiching the body between an aluminum strap and the floor.
Well nuts and bolts will sandwich the floor between the frame and another aluminum strap. At least 2 outriggers will support the body and floor outside the frame rails, and 2 crossmembers will support the floor inside the frame rails.
The cowl will be supported by a 1.5" OD tubing hoop that will support the steering column and the door hinges. The rear of the body will gave additional support about half way up with mounts at the top of each Kickup.
My main support concern is lateral at the rear of the door openings...but then what do I know <shrug>
Thanks. The Kudos should rightfully go to my late dad. He's the one responsible for instilling the life lesson of doing with what you have, unless you can afford to do otherwise...and complaining will only get you the disdain of others.I like your comment about having to play the cards you have been delt. Yeah you could whine about it but the attitude you have is much more constructive . Kudos...
There is a thing called polymorph. Its beads of plastic that go soft when put into boiling water and then cools to a hard plastic. I used it to form a sanding profile on a bit of swage line that was correct and then after cooling it became the backing block for the rest of the contour lines on the body. Its only about 10 bucks for a pack and can be remelted and reformed again and again. Saves on wood and routing.
Have a look on UTub for ideas. I have found a few uses for it besides the above. It can be file'd, drilled and tapped once hard. Useful stuff to have around.
G
I'll post some pics soon, I am currently fixing a screw up and not thrilled about it, pics will remind me, lol. I don't think they are better, the bear claw are stronger, in my opinion, but the model t hinges don't have the post pertruding from the door jamb and that's important to me. Latch part number tel:16-55849-1 strike part number tel:16-55854-1 at macsautoparts.com. I tried to copy and paste pics, no luck. Sorry! These do pertrude a little, but I don't think they will cause as much grief entering and exiting. They are similar to the bear claw because they also allow for vertical support as well as horizontal as the strike fits inside of the latch. I didn't make my doors very thick because I am trying to preserve as much me space as possible, so I don't have room for the bear claws unless I go with the minis that are basically for trunks. I was going to use the surface mount latches, but don't like them pertruding on the inside of the door and they don't provide any vertical support. The t latches seem the best option for my particular application. I would strongly reccomend researching all details prior to beginning the door project. I would have done things a little different looking back. You can spend a lot of money pretty quick on hinges, latches, etc, so shop and compare your options. I did get out to the shop today for a while and just about have my screw up corrected. Now that I'm back into it, things should go more smoothly, I hope! At least my glass and related resin and putty is still good. Too bad I had to screw up to find out.... my auto biography! I'm no sissy, I do everything the hard way...is that good?Can we see the strikes? Are they better than using Bearclaw latches?