I am to the point of trying to work out the detailed dimensions of my frame for the CAD file going to the shop that will make the frame. The components I'm using are all Speedway, but the components were purchased individually, not as a kit. What I have is a 5" drop tube axle, spring over axle adjustable perches, a mono-leaf spring, 4-bar bat wings, under axle perch bolt mounted shock mounts, F1 shock mounts for the frame, and polished SS 4-bars with 7° welded ends on one end of each bar and heims on the other ends. For the frame I'm planning on 4"x2" 1/8 wall tube for the rails, and 4"x2" 3/16" wall tube for the front and rear crossmembers.
The first issue is one of never having seen it done that way. The front spring perches on square/rectangular frame rails I've seen all fasten to the front and top of the crossmember. Would there be a problem with wrapping the perch around the back of the crossmember instead of the front? I'm planning on 3/8" material for the perch, the bottom of the spring mounting plate being somewhere around 2" to 2-1/2" above the crossmember. A 1-3/4" wide tongue will wrap around the back of the crossmember. I'm also considering wrapping the perch around the underside of the frame rail, if needed. The reason for all of this is 2-fold. The grille shell I have is constructed similar to a '32 Ford shell, but I do not want to chop off the bottom of the shell, as is frequently done on T-Buckets with '32 shells. What I want to do is trim back the sides on the bottom of the shell, leaving the front as an apron that will be between the crossmember and the axle and spring. The general look I'm going for is something like Jim Stroupe's car
...with the spring perch passing through the grille, and the spring and axle being in front of the shell and grille. The 2nd part of the problem comes from the rack & pinion being right behind the crossmember, with no wiggle room. There is no room to move the crossmember back and have room for the perch to wrap around the front of the crossmember. As is, the back side of the grille mesh will be right against the front of the crossmember, and there is going to be some bracket contortions to get the R&P mounted on the back side of the crossmember.
The next issue is determining the height of the spring perch. I've seen at least a couple ways to determine the final amount of spring sag under load, with multi-leaf springs, and the typical weight of a V8 in the front end. Where the problem comes in is that I have a mono-leaf spring and an engine that weighs 200-250 lbs less than a SBC. The most exact recommendation I've run across for a multi-leaf and small block v8 set up said to expect around an 1-1/2" sag. Is the amount of under load sag for a given load and a mono-leaf about the same as a multi-leaf spring? Should I just use the 1-1/2" figure, and just adjust the expected sag proportionally to the weights of the engines? The spring came with a 1/4" shim. Is that 1/4" shim the expected compensation for going from a multi-leaf to a single-leaf?
Another big issue at the moment is the positioning of the frame end attachment points for the front 4-bars. A big part of the problem comes from the problem above...not knowing the positioning of the front axle relative to the frame. Another part of the complication come from the caster angle of the axle...I'd like to build in a 7° caster angle. The last (as far as I know) point of complication is the angle of the 4-bars relative to the frame. The configuration I'm using is as described in this NTBA chassis tech page post National T-Bucket Alliance - Login
The attachment points will be tubes welded into notches on the top and bottom of the frame rail. I can use a tape measure and some math to get "on paper" locations, but I know that on paper and reality frequently do not agree.
Any help on any or all of these issues will be greatly appreciated.
The first issue is one of never having seen it done that way. The front spring perches on square/rectangular frame rails I've seen all fasten to the front and top of the crossmember. Would there be a problem with wrapping the perch around the back of the crossmember instead of the front? I'm planning on 3/8" material for the perch, the bottom of the spring mounting plate being somewhere around 2" to 2-1/2" above the crossmember. A 1-3/4" wide tongue will wrap around the back of the crossmember. I'm also considering wrapping the perch around the underside of the frame rail, if needed. The reason for all of this is 2-fold. The grille shell I have is constructed similar to a '32 Ford shell, but I do not want to chop off the bottom of the shell, as is frequently done on T-Buckets with '32 shells. What I want to do is trim back the sides on the bottom of the shell, leaving the front as an apron that will be between the crossmember and the axle and spring. The general look I'm going for is something like Jim Stroupe's car
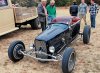
The next issue is determining the height of the spring perch. I've seen at least a couple ways to determine the final amount of spring sag under load, with multi-leaf springs, and the typical weight of a V8 in the front end. Where the problem comes in is that I have a mono-leaf spring and an engine that weighs 200-250 lbs less than a SBC. The most exact recommendation I've run across for a multi-leaf and small block v8 set up said to expect around an 1-1/2" sag. Is the amount of under load sag for a given load and a mono-leaf about the same as a multi-leaf spring? Should I just use the 1-1/2" figure, and just adjust the expected sag proportionally to the weights of the engines? The spring came with a 1/4" shim. Is that 1/4" shim the expected compensation for going from a multi-leaf to a single-leaf?
Another big issue at the moment is the positioning of the frame end attachment points for the front 4-bars. A big part of the problem comes from the problem above...not knowing the positioning of the front axle relative to the frame. Another part of the complication come from the caster angle of the axle...I'd like to build in a 7° caster angle. The last (as far as I know) point of complication is the angle of the 4-bars relative to the frame. The configuration I'm using is as described in this NTBA chassis tech page post National T-Bucket Alliance - Login
The attachment points will be tubes welded into notches on the top and bottom of the frame rail. I can use a tape measure and some math to get "on paper" locations, but I know that on paper and reality frequently do not agree.
Any help on any or all of these issues will be greatly appreciated.