Gerry
Well-Known Member
There are several things that can cause undercut but mostly it occures when the torch angle is incorrect. The key to solving this problem IMO is watching and working the puddle to fiil the crater from the arc. Excessive speed is the culprit for many welders also.
Russ you are correct about the stress along the side of a weld however most of the failures I've seen in that area are from a cold lap to the base metal. Again controling the puddle will help. If you don't see the base metal fuse into the fillermetal, chances are good a cold lap will result.
Consistant good welds require 3 things ... practice, practice and more practice.
Ron
heres one on my engine mount done with sick. Not critical and ready for dressing. If you look carefully at the short weld you can see where I moved a little too fast. Old eyes again Im afraid
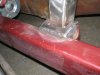
G