meangreen
Active Member
Hackerbilt and James C. - George's (fluidfloyd) description is correct (above). Whether there is room under a Bucket for a truck arm system would depend on the length of the frame and, more specifically, the distance from the rear axle to the forward mounting point (usually at or near the transmission crossmember). I have truck arm style rear suspension under my coupe. I have attached an early construction pic of it so you can see the configuration. Mine are considerably shorter than original Chevy truck arms, but the car still rides and handles great. Mine are rubber mounted at the rear so the suspension can move without flexing the arms or twisting the axle housing. In most Buckets, the engine is too close to the rear end to make it practical. However, if you run them straight forward and attach them under the frame rails, they work great. In that configuration they are usually called "lift bars". Smokeyco is building a set of them on his thread "My First T Build". Take a look at them.
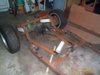
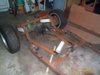