Indycars
Well-Known Member
I'm converting from a 2-bend axle with drum brakes to a 4-bend axle with disc brakes. It makes sense to order everything from one place so if something does not fit, it will be easy to remedy the problem, everything will be coming from Speedway. It presently has 1962 Econoline spindles and brakes that will need a new home in the near future.
The components ordered are .....
Spring Over Front Tube Axle, Chevy Spindle, 4 Inch Drop, Plain
Plain Chevy Wilwood Front Brake & Tradit. Steering Kits, 48 Inch Axle
Wilwood 150-8850K 7112 BP-10 Brake Pad Set, DLIII/BDL/FDL, .49 Inch
Super Glide® T-Bucket Front Spring, Standard Eye, Plain
Speedway Stainless 1-3/4 Inch Leaf Spring Front Suspension Pivot
Transverse Leaf Spring Shackles w/ Nylon Bushings, Stainless
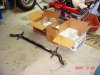
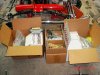
I'm trying to stay with my manual 1" MC, so that's why I went with the 4 piston Wilwood caliper. My thinking was they will have more stopping power over the 2 piston or even the single piston, making up for the required higher pressures of a disc brake. If this doesn’t work like I need, then there is a proportioning valve. Test, make changes, restest.
This Single Piston GM caliper 4.4 SqIn [ I think is also an option ]
1978-88 GM Metric G-Body Brake Calipers, IMCA Approved, 7/16-20
Wilwood Disc Brakes - Caliper Part No: 120-8925
2 – Piston Caliper Piston Area = 2.4 SqIn [ This was an Option ]
Wilwood Disc Brake Kit 1949-54 Chevy Spindles, 2-Piston, Steel Rotor
Wilwood Disc Brakes - Caliper Part No: 120-10188
4 – Piston Caliper Piston Area = 4.8 SqIn [ My Calipers ]
Forged Dynalite-1.75/.380
Wilwood Disc Brakes - Caliper Part No: 120-6818
If you need to take a deep dive into brakes and enjoy numbers then this website is your place. You can download his Excel spreadsheet or I have included it below after I modified it to include an the addition of a 2nd system so you can compare two systems side-by-side.
BillaVista.com-Brake Bible Tech Article by BillaVista
If you want to download the Excel file from his website, this is what you are looking for. It’s a very long web page.
The components ordered are .....
Spring Over Front Tube Axle, Chevy Spindle, 4 Inch Drop, Plain
Plain Chevy Wilwood Front Brake & Tradit. Steering Kits, 48 Inch Axle
Wilwood 150-8850K 7112 BP-10 Brake Pad Set, DLIII/BDL/FDL, .49 Inch
Super Glide® T-Bucket Front Spring, Standard Eye, Plain
Speedway Stainless 1-3/4 Inch Leaf Spring Front Suspension Pivot
Transverse Leaf Spring Shackles w/ Nylon Bushings, Stainless
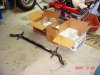
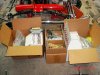
I'm trying to stay with my manual 1" MC, so that's why I went with the 4 piston Wilwood caliper. My thinking was they will have more stopping power over the 2 piston or even the single piston, making up for the required higher pressures of a disc brake. If this doesn’t work like I need, then there is a proportioning valve. Test, make changes, restest.
This Single Piston GM caliper 4.4 SqIn [ I think is also an option ]
1978-88 GM Metric G-Body Brake Calipers, IMCA Approved, 7/16-20
Wilwood Disc Brakes - Caliper Part No: 120-8925
2 – Piston Caliper Piston Area = 2.4 SqIn [ This was an Option ]
Wilwood Disc Brake Kit 1949-54 Chevy Spindles, 2-Piston, Steel Rotor
Wilwood Disc Brakes - Caliper Part No: 120-10188
4 – Piston Caliper Piston Area = 4.8 SqIn [ My Calipers ]
Forged Dynalite-1.75/.380
Wilwood Disc Brakes - Caliper Part No: 120-6818
If you need to take a deep dive into brakes and enjoy numbers then this website is your place. You can download his Excel spreadsheet or I have included it below after I modified it to include an the addition of a 2nd system so you can compare two systems side-by-side.
BillaVista.com-Brake Bible Tech Article by BillaVista
If you want to download the Excel file from his website, this is what you are looking for. It’s a very long web page.