Kaaso
Member
Hey guys just wanted to say HI and let ya know we have made some great progress in a short time. We built a wooden jig to set up the frame rails. Once those were tacked we built 2 small jigs to help set up the layout of the frame. Yesterday we were able to get the whole frame tacked up and ready to be fully welded. Since I dont have a welder big enough to do the job, I am going to take the frame to a friends house this coming weekend to weld it all up. I have the body, turtle deck, steering box and most of the front suspension already purchased. So I have plenty to keep me busy for a while.
Guys, please understand this is my first street rod build and I have and will make plenty of mistakes. I do have my brother and a friend who are helping out, both to whom I owe a big thanks for their help thus far. Thanks for listening to my story and we will keep in touch.:tip:
Sorry about the large pics, I will resize smaller next time.
Guys, please understand this is my first street rod build and I have and will make plenty of mistakes. I do have my brother and a friend who are helping out, both to whom I owe a big thanks for their help thus far. Thanks for listening to my story and we will keep in touch.:tip:
Sorry about the large pics, I will resize smaller next time.
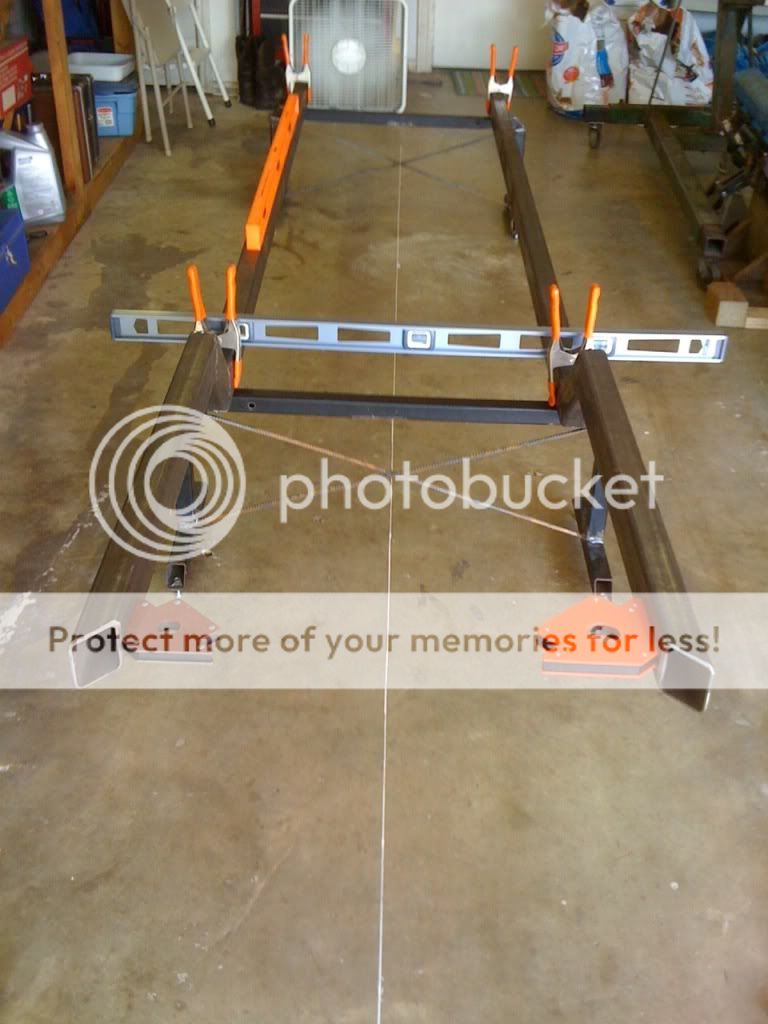
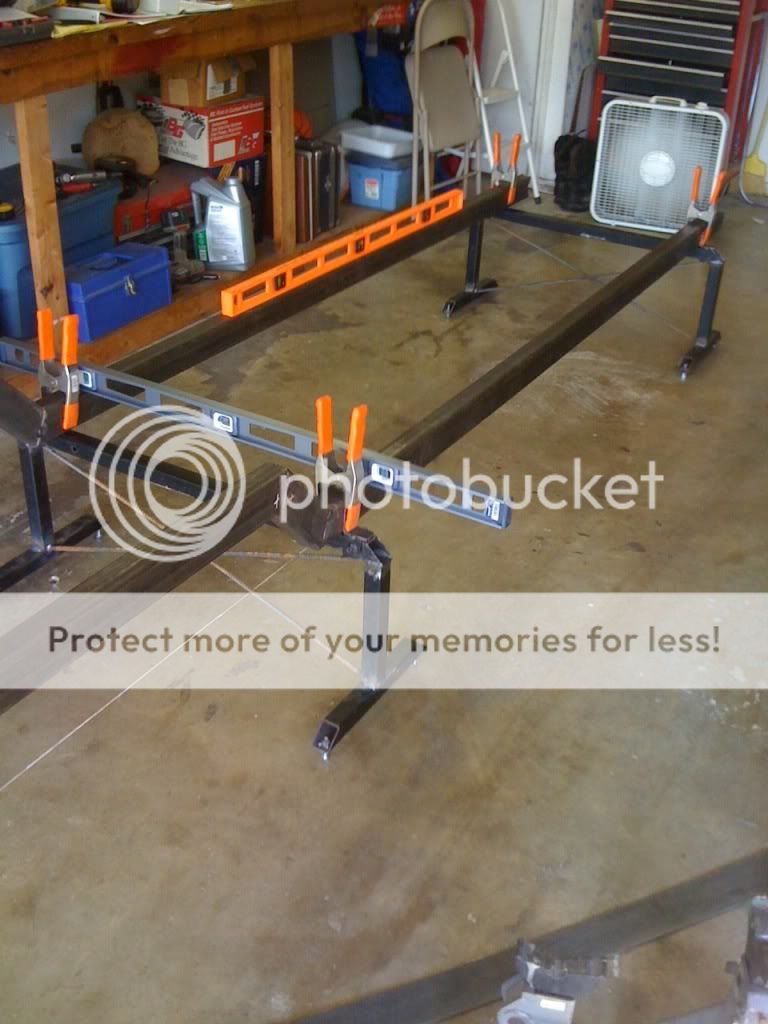
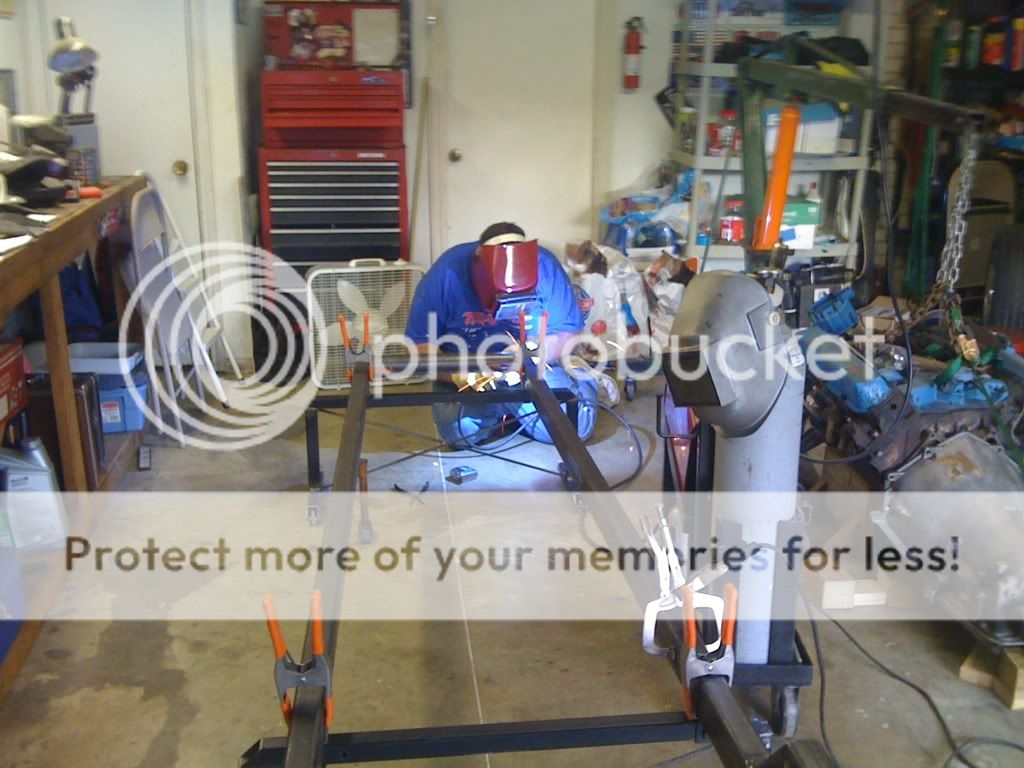
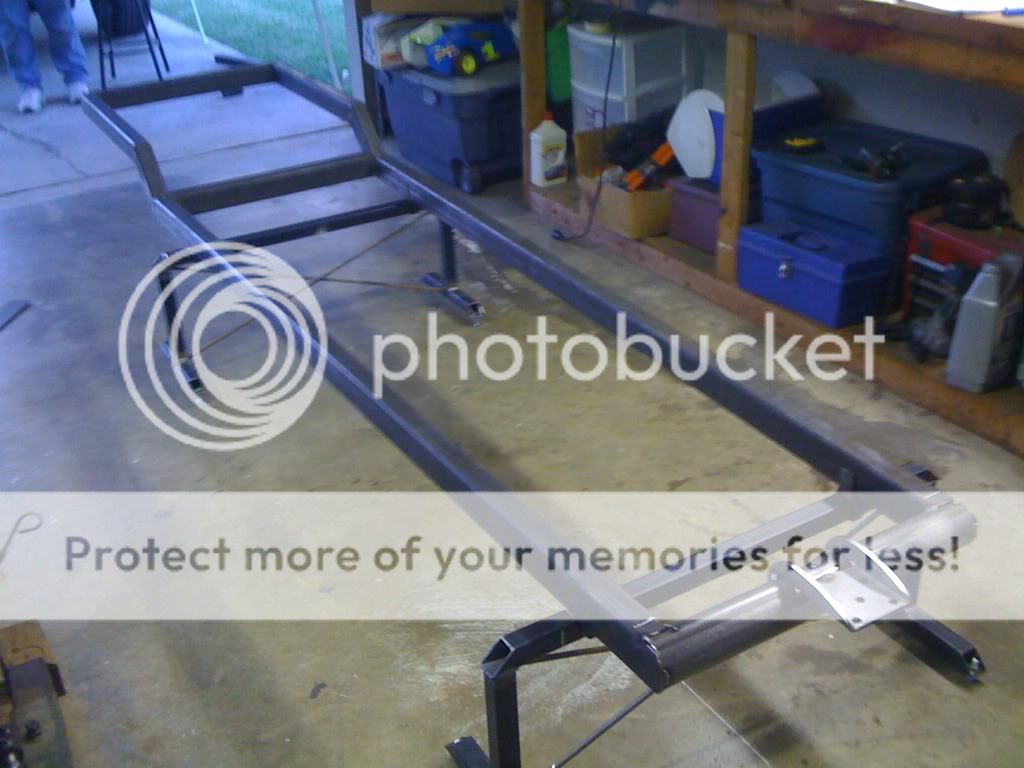
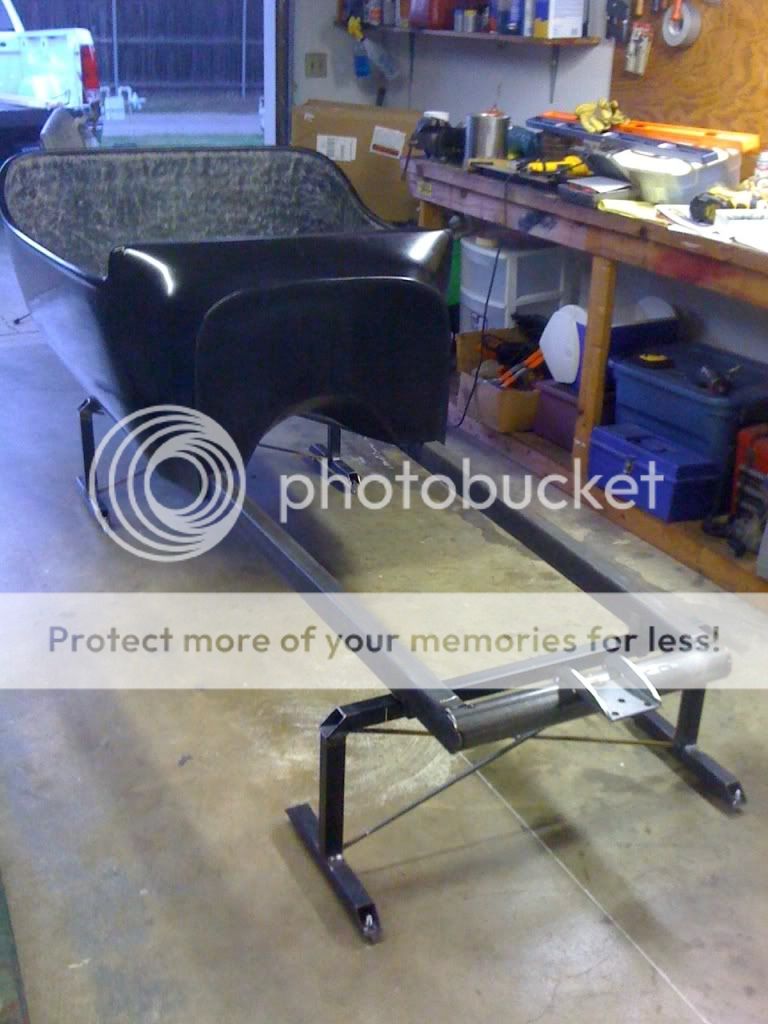
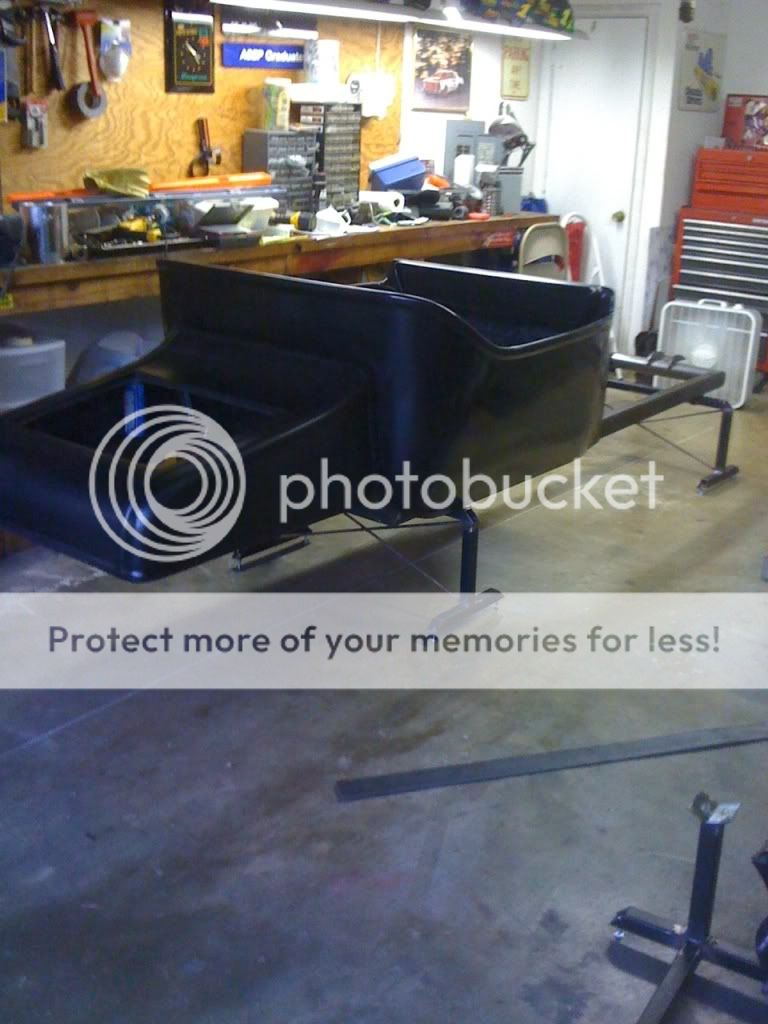