Using stainless steel sounds like a great idea, but it’s more complicated because of the available sizes of stainless to choose from. On T-buckets, the most common radius rods are made using steel tubing 7/8” x .156” wall with an ID of .563” or 7/8” x .188” wall with an ID of .499”. A 5/8” x 18 thread is normally used for the heims joint or clevis. A 5/8”x18 thread calls for a 37/64” (.578”) drill. Both of the above-mentioned sizes work great for this.
7/8” stainless tubing typically is only available in only .065” or .120” wall thickness. The .120” wall is .635 ID which is too big to tap a 5/8 x 18 thread. The .065 wall could be used with a threaded tube end, but it most likely wouldn’t be strong enough. A solid 7/8” stainless bar could be threaded and used if you are not worried about the weight.
If you increased the radius rod size to 1”, stainless tubing is available in 1” x .250” wall thickness. It has an ID of ½” which you could drill and tap for a 5/8”x18 thread like 409 suggested. Both the .120” and .188” wall have too large of an ID to tap and don’t have the room for a threaded rod end.
Most of the threaded rod ends are just tapered, but there are a few companies like Chassis Shop and Meziere that make a 4130 left hand thread with a hex on the threaded rod end. I’m not aware of anyone selling them in stainless steel.
As was mentioned, a stainless nut could be welded to tubing, but I would be very worried about trusting the strength of a butt weld on a radius rod. Typically, in addition to welding top of the tubing to the threaded tube end, a hole is drilled through the tube on both side and then rosette welded for additional strength.
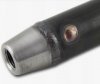