I have bolt-in round tube transmission crossmember mounts like these...
They are made for 3/8" mounting bolts. The transmission that will be mounted is a 700R4...the engine a light weight V6, weighing around 200 lbs less than a SBC. The crossmember will float inside the cups, so there will be no torquing or pulling forces on the brackets...only weight support. My question is would 3/8" Nutserts be sufficient for fastening these mounts to the frame rails?
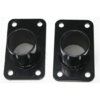
They are made for 3/8" mounting bolts. The transmission that will be mounted is a 700R4...the engine a light weight V6, weighing around 200 lbs less than a SBC. The crossmember will float inside the cups, so there will be no torquing or pulling forces on the brackets...only weight support. My question is would 3/8" Nutserts be sufficient for fastening these mounts to the frame rails?